Multifunctional automatic guide transport vehicle
An automatic guidance and multi-functional technology, applied in the direction of hoisting devices, etc., can solve the problems of increased cost of non-standard services, unreliable domestic performance, high repair and maintenance costs, etc., to reduce dependence on foreign technology or products, and compact structure , the effect of high degree of automation
- Summary
- Abstract
- Description
- Claims
- Application Information
AI Technical Summary
Problems solved by technology
Method used
Image
Examples
Embodiment Construction
[0049] figure 1 It is a schematic structural diagram of a multifunctional automatic guided transport vehicle according to an embodiment of the present invention. Such as figure 1 shown and refer to Figure 2 to Figure 5 , the embodiment of the present invention provides a multifunctional automatic guided transport vehicle. A multifunctional automatic guided transport vehicle is characterized in that it includes a vehicle body 20, a vehicle drive system 30, a multi-point jacking device 40, a bus system and a safety guiding device.
[0050] The vehicle body 20 has a chassis 21 , a column 22 mounted on the front end of the chassis 21 , and a top cover 23 mounted on the top of the column 22 . The chassis 21 has two fork legs arranged in parallel. The insertion end of each prong is the rear end of the vehicle body 20 . Each fork has a fork base frame 211 and a tray 50 disposed on the upper side of the fork base frame 211 . The column 22 is sequentially provided with a battery...
PUM
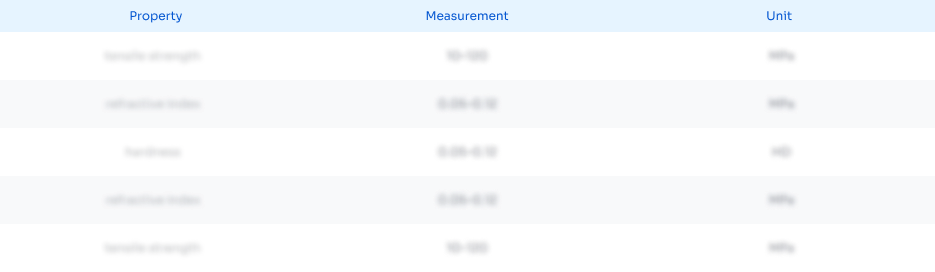
Abstract
Description
Claims
Application Information

- R&D
- Intellectual Property
- Life Sciences
- Materials
- Tech Scout
- Unparalleled Data Quality
- Higher Quality Content
- 60% Fewer Hallucinations
Browse by: Latest US Patents, China's latest patents, Technical Efficacy Thesaurus, Application Domain, Technology Topic, Popular Technical Reports.
© 2025 PatSnap. All rights reserved.Legal|Privacy policy|Modern Slavery Act Transparency Statement|Sitemap|About US| Contact US: help@patsnap.com