Positioning adjustment mechanism
A positioning adjustment and adjustment mechanism technology, which is applied to metal processing machinery parts, automatic control devices, measuring/indicating equipment, etc., can solve the problems of inability to achieve stop and stop effects, instability, and impact resistance, etc., to facilitate equipment inspection and equipment maintenance, improve the speed of installation and debugging, and the effect of simple structure
- Summary
- Abstract
- Description
- Claims
- Application Information
AI Technical Summary
Problems solved by technology
Method used
Image
Examples
Embodiment 1
[0041] combine figure 1 and figure 2As shown, a positioning adjustment mechanism includes a mandrel 1, a rough positioning mechanism 2, a precise positioning mechanism 3 and a buffer force adjustment mechanism 4; the rough positioning mechanism 2 is provided with an axial through hole, and the mandrel 1 and the buffer force The force adjustment mechanism 4 is arranged in the through hole; the precise positioning mechanism 3 is set on the rough positioning mechanism 2, and forms a micrometer-like structure with the rough positioning mechanism 2; the buffer force adjusting mechanism 4 is connected to the above-mentioned mandrel 1 , and is used to buffer the pressure impact of the stop of the target tooling 5.3; the mandrel 1 supports the rough positioning mechanism 2, the rough positioning mechanism 2 roughly sets the stop position of the target tooling 5.3, and the fine positioning mechanism 3 is further finely adjusted The target tooling 5.3 stop position; thus, the position...
Embodiment 2
[0051] to combine image 3 As shown in the specific usage of the positioning adjustment mechanism of the present invention, embodiment 2 shows a specific working process of the coarse positioning adjustment mechanism of the present invention as follows: in embodiment 2, according to actual production needs, the target tooling 5.3 is driven by the cylinder 5.2 Moving on the screw rod 5.4, the positioning adjustment mechanism is fixed on the stop block 5.1; the positioning adjustment mechanism cooperates with the coarse positioning sleeve 2.1 in the coarse positioning mechanism 2 and the coarse positioning lock nut 2.2, and the approximate position where the target tooling 5.3 stops is roughly predetermined. as attached image 3 In the position a shown, the cylinder 5.2 drives the target tooling 5.3 to slide on the screw rod 5.4, and the left side contacts the buffer head 4.1, guided by the mandrel 1, and transmits the pressure of the target tooling 5.3 to the buffer spring 4.2,...
PUM
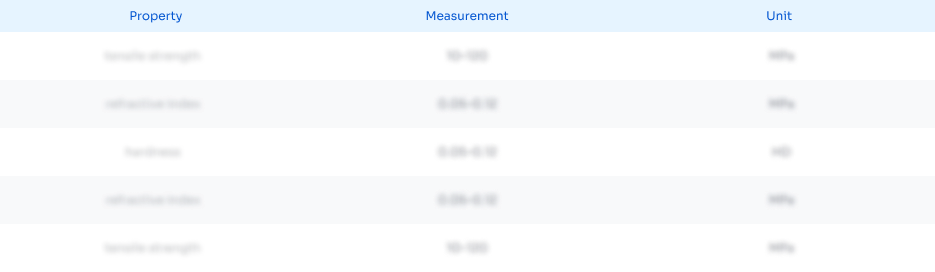
Abstract
Description
Claims
Application Information

- Generate Ideas
- Intellectual Property
- Life Sciences
- Materials
- Tech Scout
- Unparalleled Data Quality
- Higher Quality Content
- 60% Fewer Hallucinations
Browse by: Latest US Patents, China's latest patents, Technical Efficacy Thesaurus, Application Domain, Technology Topic, Popular Technical Reports.
© 2025 PatSnap. All rights reserved.Legal|Privacy policy|Modern Slavery Act Transparency Statement|Sitemap|About US| Contact US: help@patsnap.com