Friction material, brake pad made thereof and method for manufacturing brake pad
A technology of friction materials and brake pads, applied in friction linings, gear transmission mechanisms, mechanical equipment, etc., can solve problems such as limited high temperature resistance and thermal recession, achieve reduced density, light relative density, and improved impact resistance sexual effect
- Summary
- Abstract
- Description
- Claims
- Application Information
AI Technical Summary
Problems solved by technology
Method used
Image
Examples
Embodiment 1
[0029] This embodiment 1 provides a friction material whose raw materials include the following components:
[0030] Steel fiber 150g, brass fiber 200g, mineral fiber 20g, nitrile rubber modified phenolic resin 30g, flake graphite 30g, petroleum coke 140g, molybdenum disulfide 10g, alumina 50g, chromite 30g, cast iron powder 60g, zinc powder 50g, 100g of ferric oxide, 40g of elastic particles, 30g of barium sulfate, and 60g of vermiculite.
[0031] The method for manufacturing a brake pad by using the above-mentioned friction material includes the following steps:
[0032] Weigh the above-mentioned raw material components and mix them uniformly to form a mixture; place the mixture in a mold, press at 16MPa and 155°C for 10s to obtain a brake pad blank, and then heat the obtained blank to 220°C for solidification 14h, the brake pad A was prepared.
Embodiment 2
[0034] Embodiment 2 provides a friction material whose raw materials include the following components:
[0035] Steel fiber 120g, brass fiber 240g, mineral fiber 25g, nitrile rubber modified phenolic resin 20g, flake graphite 20g, petroleum coke 170g, molybdenum disulfide 8g, alumina 40g, chromite 40g, cast iron powder 50g, zinc powder 40g, 120g of ferric oxide, 50g of elastic particles, 20g of barium sulfate, 70g of vermiculite.
[0036] The method for manufacturing a brake pad by using the above-mentioned friction material includes the following steps:
[0037] Weigh the above-mentioned raw material components and mix them uniformly to form a mixture; place the mixture in a mold, press at 20MPa and 155°C for 5s to obtain a brake pad blank, and then heat the obtained blank to 220°C for solidification 14h, the brake pad B was prepared.
Embodiment 3
[0039] Embodiment 3 provides a friction material whose raw materials include the following components:
[0040]Steel fiber 180g, brass fiber 160g, mineral fiber 15g, nitrile rubber modified phenolic resin 35g, flake graphite 40g, petroleum coke 110g, molybdenum disulfide 5g, alumina 60g, chromite 20g, cast iron powder 45g, zinc powder 60g, 80g of ferric oxide, 30g of elastic particles, 40g of barium sulfate, 45g of vermiculite.
[0041] The method for manufacturing a brake pad by using the above-mentioned friction material includes the following steps:
[0042] Weigh the above-mentioned raw material components and mix them uniformly to form a mixture; place the mixture in a mold, press at 15MPa and 160°C for 5s to obtain a brake pad blank, and then heat the obtained blank to 250°C for solidification 12h, the brake pad C was prepared.
PUM
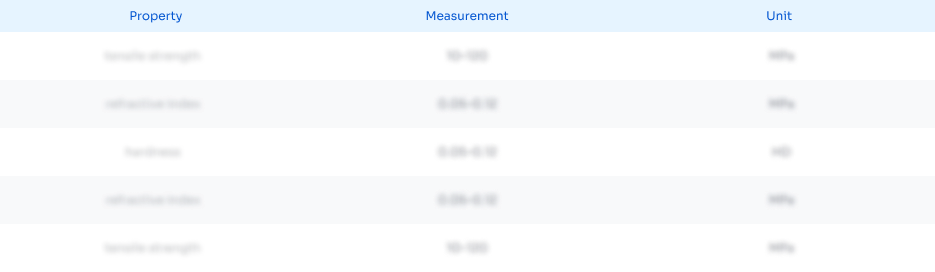
Abstract
Description
Claims
Application Information

- R&D
- Intellectual Property
- Life Sciences
- Materials
- Tech Scout
- Unparalleled Data Quality
- Higher Quality Content
- 60% Fewer Hallucinations
Browse by: Latest US Patents, China's latest patents, Technical Efficacy Thesaurus, Application Domain, Technology Topic, Popular Technical Reports.
© 2025 PatSnap. All rights reserved.Legal|Privacy policy|Modern Slavery Act Transparency Statement|Sitemap|About US| Contact US: help@patsnap.com