FPGA-based SOPC multi-axis linkage motion controller and control system
A technology of motion controller and multi-axis linkage, applied in general control system, control/adjustment system, program control, etc., can solve the problems of low speed regulation efficiency of motion control system, prolong the upgrade cycle, increase the upgrade cost, etc., and achieve Achieve hardware and customization, speed up the development cycle, and improve efficiency
- Summary
- Abstract
- Description
- Claims
- Application Information
AI Technical Summary
Problems solved by technology
Method used
Image
Examples
Embodiment 1
[0037] figure 1 It is a schematic structural diagram of Embodiment 1 of an FPGA-based SOPC multi-axis linkage motion controller of the present invention.
[0038] Such as figure 1 As shown, an FPGA-based SOPC multi-axis linkage motion controller of the present invention includes a storage module, a soft IP and a multi-axis linkage motion control module.
[0039] Such as figure 2 As shown, the multi-axis linkage motion control module is configured to execute the following procedures:
[0040] Set the initial processing point of the line segment that can be continuously processed as the origin in the X, Y, and Z three-axis coordinate system;
[0041] Obtain the coordinate information of the current processing point relative to the origin in the line segment that can be processed continuously;
[0042] Obtain the vector virtual long axis in real time, where the vector direction of the virtual long axis is from the origin to the current processing point, and the vector size of the virtual ...
Embodiment 2
[0060] Such as image 3 As shown, an FPGA-based SOPC multi-axis linkage motion controller of the present invention includes a storage module, a soft IP, a multi-axis linkage motion control module and an IO module.
[0061] Among them, the working principle of the multi-axis linkage motion control module is as follows figure 2 Shown.
[0062] In a specific implementation, the IO module includes a zero return input module, and the zero return input module is used to receive an external mechanical zero return signal to realize the processing equipment returning to the mechanical origin.
[0063] In another embodiment, the IO module further includes a stepper motor control output module, which is connected to the multi-axis linkage motion control module and directly drives the stepper motor through the stepper motor subdivision driver.
[0064] Specifically, the stepper motor control output module includes multiple output units with the same principle and controlled by pulses and directio...
PUM
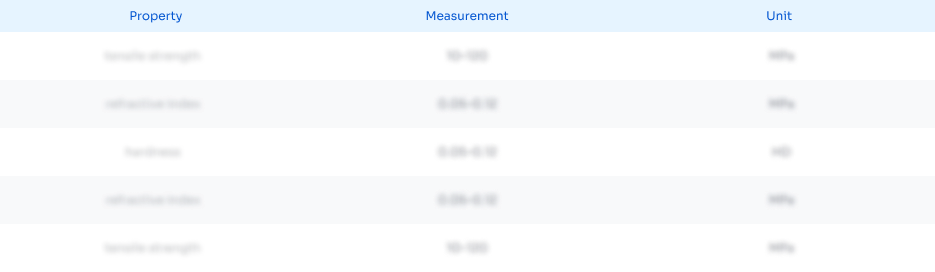
Abstract
Description
Claims
Application Information

- Generate Ideas
- Intellectual Property
- Life Sciences
- Materials
- Tech Scout
- Unparalleled Data Quality
- Higher Quality Content
- 60% Fewer Hallucinations
Browse by: Latest US Patents, China's latest patents, Technical Efficacy Thesaurus, Application Domain, Technology Topic, Popular Technical Reports.
© 2025 PatSnap. All rights reserved.Legal|Privacy policy|Modern Slavery Act Transparency Statement|Sitemap|About US| Contact US: help@patsnap.com