A method of reusing anaerobic digestion effluent and distiller's grains to produce ethanol
A technology of anaerobic digestion and distiller's grains, applied in biofuel, fermentation and other directions, can solve the problems of poisoning ethanol fermentation yeast, increase operation and cost, reduce the utilization rate of raw materials, etc., to improve process hygiene, increase utilization rate of raw materials, and avoid ethanol Effects of fermentation acidity problems
- Summary
- Abstract
- Description
- Claims
- Application Information
AI Technical Summary
Problems solved by technology
Method used
Image
Examples
Embodiment 1
[0075] A method for producing ethanol by reusing anaerobic digestion effluent and distiller's grain clear liquid of the present invention adopts the following process steps:
[0076] The membrane filtrate and distiller's grains clear liquid are mixed according to the ratio of 70:40, and the concentration of volatile acid is 600mg / L; 100Kg of pulverized corn flour is taken and 300L of mixed solution is added as ingredients, and high-temperature-resistant α-amylase (10U / g starch) is added, After stirring evenly, heat to 86°C and maintain it for 200min; cool down to 60°C, add glucoamylase (180U / g starch), stir well, and keep warm for saccharification for 30min. After the saccharification is completed, the temperature is lowered to 30° C., and 15% (v / v) yeast seed liquid is inserted to start fermentation. After fermentation, ethanol and distillation waste liquid are obtained through distillation. The distillation waste liquid is filtered with a 60-mesh filter cloth to obtain the ...
Embodiment 2
[0079] A method for producing ethanol by reusing anaerobic digestion effluent and distiller's grain clear liquid of the present invention adopts the following process steps:
[0080] The membrane filtrate and distiller's grains were mixed according to the ratio of 80:20, and the concentration of volatile acid was 300mg / L; the brown rice flour after 100Kg pulverization was added to 260L of mixed liquid ingredients, and high temperature resistant α-amylase (10U / g starch) was added, After stirring evenly, heat to 90°C and maintain for 150min; cool down to 60°C, add glucoamylase (150U / g starch), stir well, and keep warm for saccharification for 30min. After the saccharification is completed, the temperature is lowered to 30° C., and 10% (v / v) yeast seed liquid is inserted to start fermentation. After fermentation, ethanol, distillation waste liquid and fine tower residue are obtained through distillation. The distillation waste liquid is filtered with a 60-mesh filter cloth to ob...
Embodiment 3
[0083]A method for producing ethanol by reusing anaerobic digestion effluent and distiller's grain clear liquid of the present invention adopts the following process steps:
[0084] Membrane filtrate and fine tower residual liquid are mixed according to the ratio of 90:10, and the concentration of volatile acid is 100mg / L; Get the brown rice flour 1000Kg after pulverizing and add 2600L mixed solution batching, add high temperature resistant α-amylase (8U / g starch) , stir evenly, heat to 95°C and maintain for 100min; cool down to 60°C, add glucoamylase (180U / g starch), stir well, and keep warm for saccharification for 15min. After the saccharification is completed, the temperature is lowered to 30° C., and 12% (v / v) yeast seed liquid is inserted to start fermentation. After fermentation, ethanol, distillation waste liquid and fine tower residue are obtained through distillation. The distillation waste liquid is filtered with a 60-mesh filter cloth to obtain the wet distiller's...
PUM
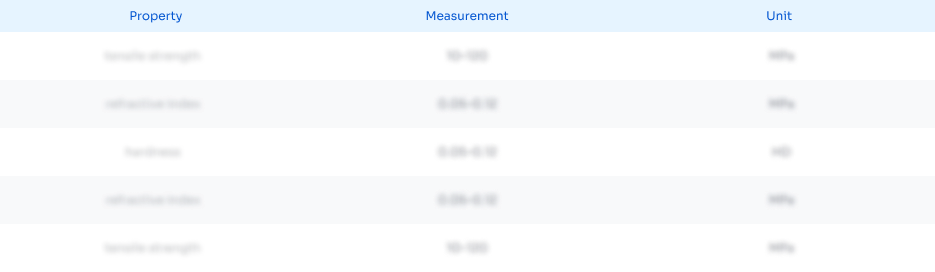
Abstract
Description
Claims
Application Information

- R&D Engineer
- R&D Manager
- IP Professional
- Industry Leading Data Capabilities
- Powerful AI technology
- Patent DNA Extraction
Browse by: Latest US Patents, China's latest patents, Technical Efficacy Thesaurus, Application Domain, Technology Topic, Popular Technical Reports.
© 2024 PatSnap. All rights reserved.Legal|Privacy policy|Modern Slavery Act Transparency Statement|Sitemap|About US| Contact US: help@patsnap.com