Method for preparing iron oxide red by utilizing iron-containing wastes and iron oxide red pigment
A technology of iron oxide red and iron hydroxide, which is applied in the field of iron oxide red pigments, can solve the problems of waste of resources, environment, pollution, etc., and achieve the effects of avoiding pollution, high economic benefits, and excellent economic value
- Summary
- Abstract
- Description
- Claims
- Application Information
AI Technical Summary
Problems solved by technology
Method used
Examples
Embodiment 1
[0034] The present embodiment provides a kind of method that utilizes iron-containing waste to prepare iron oxide red, comprises the steps:
[0035] The pickling steel pipes, seamless steel pipes, electric steel rods, thin plates and steel rolling plates of steel mills are used as raw materials, and sodium hydroxide is added to the washing liquid to completely precipitate the iron ions in the solution. Then filter to obtain a filter cake, take 500g of the filter cake and place it in an incubator, and dry it at a constant temperature for 5 hours in the presence of oxygen at 120°C to obtain 149g of dry iron hydroxide powder; place the dry iron hydroxide powder in a high-temperature-resistant vessel, and then transfer Into the crystal transformation furnace, dehydration in the molecule under the airtight condition of 400°C for 180min, transferred out of the crystal transformation furnace to cool, and standardized to obtain 111g of iron oxide red pigment. 149g iron hydroxide shoul...
Embodiment 2
[0037] The present embodiment provides a kind of method that utilizes iron-containing waste to prepare iron oxide red, comprises the steps:
[0038] The pickling steel pipes, seamless steel pipes, electric steel rods, thin plates and steel rolling plates of steel mills are used as raw materials, and sodium hydroxide is added to the washing liquid to completely precipitate the iron ions in the solution. Then filter to obtain a filter cake, take 600g of the filter cake and place it in an incubator, and dry it at a constant temperature for 3 hours in the presence of oxygen at 180°C to obtain 240g of dry iron hydroxide powder; place the dry iron hydroxide powder in a high-temperature-resistant vessel, and then transfer Into the crystal transformation furnace, dehydrated intramolecularly for 120min under the airtight condition of 450°C, transferred out of the crystal transformation furnace to cool, and standardized to obtain 178g of iron oxide red pigment. 240g iron hydroxide shoul...
Embodiment 3
[0040] The present embodiment provides a kind of method that utilizes iron-containing waste to prepare iron oxide red, comprises the steps:
[0041] The pickling steel pipes, seamless steel pipes, electric steel rods, thin plates and steel rolling plates of steel mills are used as raw materials, and sodium hydroxide is added to the washing liquid to completely precipitate the iron ions in the solution. Then filter to obtain a filter cake, get 700g of the filter cake and place it in a constant temperature box, and dry it at a constant temperature for 3.5h under the condition of 150°C in the presence of oxygen to obtain 356g of ferric hydroxide dry powder; place the ferric hydroxide dry powder in a high-temperature-resistant vessel, and then Transfer to a crystal transformation furnace, dehydrate intramolecularly for 60 minutes under airtight conditions at 600°C, transfer out of the crystal transformation furnace to cool, and standardize to obtain 265.0 g of iron oxide red pigmen...
PUM
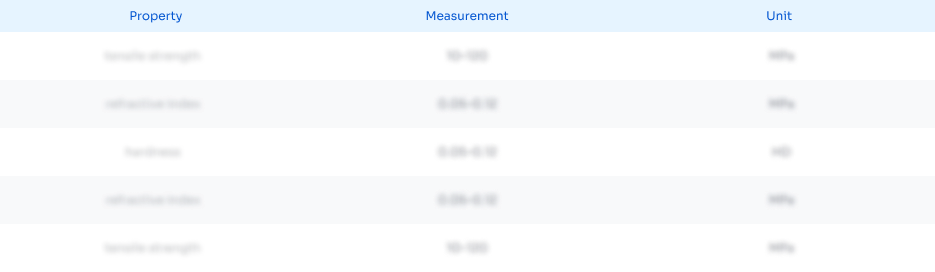
Abstract
Description
Claims
Application Information

- Generate Ideas
- Intellectual Property
- Life Sciences
- Materials
- Tech Scout
- Unparalleled Data Quality
- Higher Quality Content
- 60% Fewer Hallucinations
Browse by: Latest US Patents, China's latest patents, Technical Efficacy Thesaurus, Application Domain, Technology Topic, Popular Technical Reports.
© 2025 PatSnap. All rights reserved.Legal|Privacy policy|Modern Slavery Act Transparency Statement|Sitemap|About US| Contact US: help@patsnap.com