Five-bar linkage for aspheric component polishing
An aspheric, five-link technology, used in grinding/polishing equipment, control of workpiece feed motion, grinding frame, etc. Response, inability to effectively suppress intermediate frequency errors, etc., to achieve the effects of simple and reliable mechanism control, shortened measurement time, and high reliability
- Summary
- Abstract
- Description
- Claims
- Application Information
AI Technical Summary
Problems solved by technology
Method used
Image
Examples
Embodiment Construction
[0045] The preferred embodiments of the present invention will be described in detail below in conjunction with the accompanying drawings.
[0046] See figure 1 and figure 2 , figure 1 It is a schematic diagram of a five-bar linkage mechanism used for aspheric element polishing in the present invention, figure 2 It is a schematic diagram of the five-bar linkage mechanism used for polishing aspheric elements of the present invention. It can be seen from the figure that the five-bar linkage mechanism used for polishing aspheric elements in the present invention includes: a frame 1, a first spindle device 2, a first crank slide 3, a first spherical joint mechanism 4, and a first link slide 5. The first connecting rod 6, the workpiece 7, the first positioning measuring tool 8, the second positioning measuring tool 9, the floating head 10, the second connecting rod 11, the second connecting rod sliding table 12, the second ball joint mechanism 13, the second crank slide 14, s...
PUM
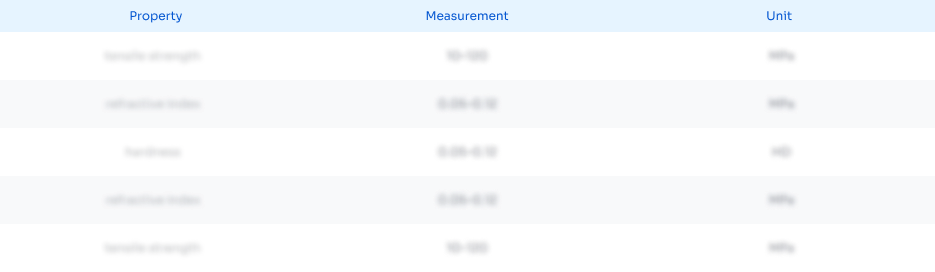
Abstract
Description
Claims
Application Information

- R&D
- Intellectual Property
- Life Sciences
- Materials
- Tech Scout
- Unparalleled Data Quality
- Higher Quality Content
- 60% Fewer Hallucinations
Browse by: Latest US Patents, China's latest patents, Technical Efficacy Thesaurus, Application Domain, Technology Topic, Popular Technical Reports.
© 2025 PatSnap. All rights reserved.Legal|Privacy policy|Modern Slavery Act Transparency Statement|Sitemap|About US| Contact US: help@patsnap.com