Inner layer pattern design method for improving copper pull during drilling
A technology of inner layer graphics and design method, applied in the direction of electrical connection formation of printing components, etc., can solve the problems of increased cutting resistance of drill bits, scrapped and enlarged boards, etc., to improve the quality of the board, reduce the scrap rate, and ensure reliability. sexual effect
- Summary
- Abstract
- Description
- Claims
- Application Information
AI Technical Summary
Problems solved by technology
Method used
Examples
Embodiment 1
[0022] This embodiment provides a method for manufacturing a PCB, which includes improving the inner layer graphic design method for drilling and pulling copper. The specific process is as follows:
[0023] (1) Cutting: Cut out the inner core board according to the panel size 520mm×620mm, the thickness of the inner core board is 0.2mm, and the thickness of the outer layer copper foil is 1OZ; according to the design requirements, reserve useful space for the inner core board The position where the hole is drilled after pressing is called the drilling position.
[0024] (2), inner layer circuit production (negative film process): inner layer graphics transfer, use a vertical coating machine to coat a photosensitive film on the inner layer core board, and the film thickness of the photosensitive film is controlled at 8 μm; - 6-grid exposure ruler (21-grid exposure ruler) completes the inner layer circuit exposure on the inner core board, transfers the inner layer graphics on the ...
Embodiment 2
[0040]This embodiment provides a method for manufacturing a PCB, especially a method for preventing copper from being pulled when drilling; the manufacturing steps of this embodiment are basically the same as those of Embodiment 1, except that steps (1) and (2) ), specifically as follows: when the thickness of the outer layer copper foil on the inner layer core plate in step (1) is less than 1OZ; the outer diameter of the ring figure in the corresponding step (2) is 0.4mm larger than the diameter of the drilled hole position.
[0041] According to the method of Example 2, 1000 PCBs were repeatedly produced, and no PCB had the problem of copper pulling when drilling holes.
Embodiment 3
[0043] This embodiment provides a method for manufacturing a PCB, especially a method for preventing copper from being pulled when drilling; the manufacturing steps of this embodiment are basically the same as those of Embodiment 1, except that steps (1) and (2) ), specifically as follows: when the thickness of the outer layer copper foil on the inner layer core plate in step (1) is greater than 2OZ; the outer diameter of the ring figure in the corresponding step (2) is 0.6mm larger than the diameter of the drilled hole.
[0044] According to the method of Example 3, 1000 PCBs were repeatedly produced, and no PCB had the problem of copper pulling when drilling holes.
[0045] In other embodiments of the present invention, according to the allowable maximum drilling deviation d / 2mm in the actual production process, the inner diameter of the ring figure is designed to be dmm smaller than the drilling position on one side (i.e. the maximum drilling deviation Twice of that); For e...
PUM
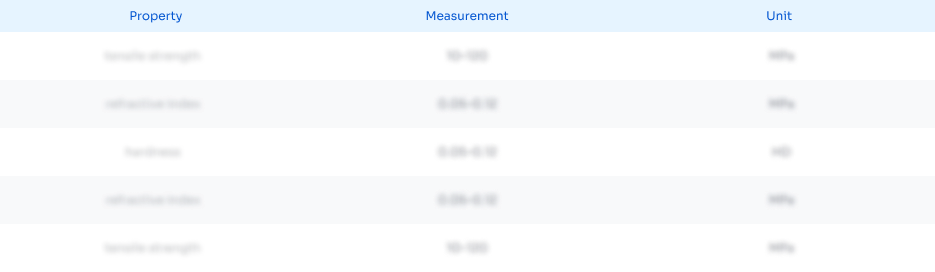
Abstract
Description
Claims
Application Information

- R&D Engineer
- R&D Manager
- IP Professional
- Industry Leading Data Capabilities
- Powerful AI technology
- Patent DNA Extraction
Browse by: Latest US Patents, China's latest patents, Technical Efficacy Thesaurus, Application Domain, Technology Topic, Popular Technical Reports.
© 2024 PatSnap. All rights reserved.Legal|Privacy policy|Modern Slavery Act Transparency Statement|Sitemap|About US| Contact US: help@patsnap.com