Fabrication method for welding module of flexible plastic substrate thin film GaAs solar cell
A flexible plastic substrate, solar cell technology, applied in circuits, photovoltaic power generation, electrical components, etc., can solve problems such as difficult operation, sidewall short circuit, battery substrate ablation, etc., to improve redundancy and improve welding. The effect of efficiency
- Summary
- Abstract
- Description
- Claims
- Application Information
AI Technical Summary
Problems solved by technology
Method used
Image
Examples
Embodiment 1
[0031] see Figure 1 ~ Figure 2 , a form of the flexible thin-film GaAs solar cell welding module of the present invention, the welding module includes: a thin-film GaAs solar cell 4 , an anisotropic conductive glue 201 , and an interconnection sheet 3 . The solar cell 4 is a thin-film gallium arsenide cell with electrodes facing upwards, including battery electrodes 1, main grid lines 11, thin grid lines 12, and a flexible plastic substrate 5; the anisotropic conductive adhesive 201 is pasted in parallel on the On the electrode surface 1 of the solar cell; the interconnection sheet 3 is pasted on the surface of the anisotropic conductive adhesive 201 in parallel to realize the connection and conduction between the electrode and the interconnection sheet.
[0032] The manufacturing method of the welding module of the thin-film gallium arsenide battery in the above-mentioned embodiment 1 is as follows:
[0033] Step one, see Figure 5 , using Hitachi Chemical’s (Hitachi Chemi...
Embodiment 2
[0043] see Figure 3 ~ Figure 4 Another form of the flexible thin film gallium arsenide solar cell welding module of the present invention is a flexible plastic substrate coplanar electrode thin film gallium arsenide battery series structure, and the welding module includes: thin film gallium arsenide solar cell 4, different Square conductive adhesive 2, interconnect sheet 3. The solar cell 4 is a thin film gallium arsenide cell with coplanar electrodes on a flexible plastic substrate, and the anisotropic conductive adhesive 201 is pasted on the surface of the electrode 1 of the solar cell 4 in parallel to realize the connection of adjacent positive and negative electrodes. The interconnection sheet 3 is pasted on the surface of the anisotropic conductive adhesive 201 in parallel, and the interconnection and conduction of adjacent battery electrodes are realized after hot pressing.
[0044] The manufacturing method of the welding module of the thin-film gallium arsenide batte...
PUM
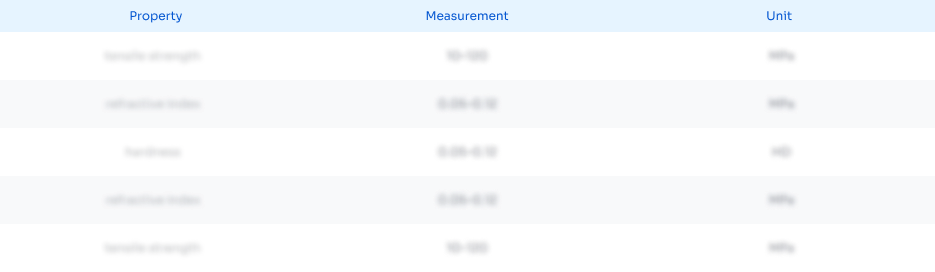
Abstract
Description
Claims
Application Information

- Generate Ideas
- Intellectual Property
- Life Sciences
- Materials
- Tech Scout
- Unparalleled Data Quality
- Higher Quality Content
- 60% Fewer Hallucinations
Browse by: Latest US Patents, China's latest patents, Technical Efficacy Thesaurus, Application Domain, Technology Topic, Popular Technical Reports.
© 2025 PatSnap. All rights reserved.Legal|Privacy policy|Modern Slavery Act Transparency Statement|Sitemap|About US| Contact US: help@patsnap.com