Method for recycling aluminum alloy casting aluminum residue
An aluminum alloy and recycling technology, which is applied in the field of comprehensive recycling of aluminum processing waste, can solve problems such as environmental pollution and waste of resources, and achieve the effects of less investment in equipment, high production efficiency, and low energy consumption
- Summary
- Abstract
- Description
- Claims
- Application Information
AI Technical Summary
Problems solved by technology
Method used
Image
Examples
Embodiment 1
[0024] Embodiment 1: as figure 1 As shown, the method for resourceful processing of the aluminum alloy casting aluminum slag, the specific steps are as follows:
[0025] Put the aluminum slag produced in the process of aluminum alloy melting and casting into the wind separator, separate the metal aluminum alloy in the aluminum slag through wind separation, then put the separated aluminum slag in the boiling furnace, and add it to the boiling furnace A mixture of sodium carbonate and calcium carbonate (the mass ratio of sodium carbonate and calcium carbonate is 1:1), in which the mass ratio of aluminum slag to the mixture of sodium carbonate and calcium carbonate is 1:4, react at 1100 °C for 3 hours, and put it in a boiling furnace Aluminum slag calcined sand is obtained at the bottom of the fluidized bed furnace, and high-temperature dust-containing flue gas is obtained at the top of the fluidized bed furnace, and then the high-temperature dust-containing flue gas is passed in...
Embodiment 2
[0027] Embodiment 2: put the aluminum slag produced in the aluminum alloy melting and casting process into the air separator, separate the metal aluminum alloy in the aluminum slag through air separation, then place the separated aluminum slag in the boiling furnace, and Add calcium carbonate into the fluidized furnace, wherein the mass ratio of aluminum slag to calcium carbonate is 1:0.2, react at 1300 ° C for 2 hours, obtain aluminum slag calcine at the bottom of the fluidized furnace, and obtain high-temperature dust-containing flue gas at the top of the fluidized furnace, and then The high-temperature dust-laden flue gas is passed into the high-temperature dust collector, and the reaction temperature of the high-temperature dust collector is controlled at 800°C. After 1 minute, the dust is obtained in the dust collection system of the high-temperature dust collector, and the dust is mixed with the aluminum slag calcined sand obtained by calcining the fluidized fluidized furn...
Embodiment 3
[0029] Embodiment 3: put the aluminum slag produced in the aluminum alloy melting and casting process into the air separator, separate the metal aluminum alloy in the aluminum slag through air separation, then place the separated aluminum slag in the boiling furnace, and Add a mixture of sodium carbonate, calcium carbonate and magnesium carbonate to the boiling furnace (the mass ratio of sodium carbonate, calcium carbonate and magnesium carbonate is 2:1:1), and the mass ratio of aluminum slag to the mixture is 1:5. React for 7 hours, get aluminum slag calcined sand at the bottom of the fluidized bed furnace, and get high-temperature dusty flue gas at the top of the fluidized bed furnace, then pass the high-temperature dusty flue gas into the high-temperature dust collector, and control the reaction temperature of the high-temperature dust collector to 800 ° C for 1 min After the dust is obtained in the dust collection system of the high-temperature dust collector, the dust is m...
PUM
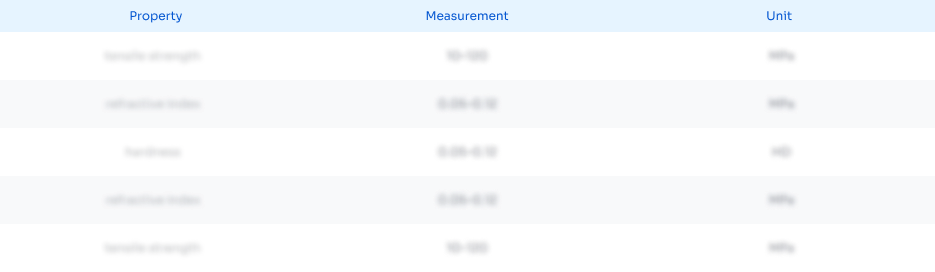
Abstract
Description
Claims
Application Information

- R&D
- Intellectual Property
- Life Sciences
- Materials
- Tech Scout
- Unparalleled Data Quality
- Higher Quality Content
- 60% Fewer Hallucinations
Browse by: Latest US Patents, China's latest patents, Technical Efficacy Thesaurus, Application Domain, Technology Topic, Popular Technical Reports.
© 2025 PatSnap. All rights reserved.Legal|Privacy policy|Modern Slavery Act Transparency Statement|Sitemap|About US| Contact US: help@patsnap.com