Flame-retardant coating for floor
A technology for flame retardant coatings and floors, applied in the field of coatings, can solve problems such as inability to meet, and achieve the effects of improving strength and toughness, preventing high temperature cracking, and improving fire performance
- Summary
- Abstract
- Description
- Claims
- Application Information
AI Technical Summary
Problems solved by technology
Method used
Image
Examples
Embodiment 1
[0019] The preparation method of flame retardant comprises the following steps:
[0020] 1) adding graphene oxide to 5wt% citric acid solution for soaking for 10 hours, and filtering to obtain acid-treated graphene oxide;
[0021] 2) Add multi-carbon nanotubes to the mixed acid solution of 10wt% dilute nitric acid and 20wt% dilute sulfuric acid, then add the acid-treated graphene oxide of step 1) for ultrasonic dispersion, filter and wash until the filtrate is neutral , to obtain a mixture of pretreated graphene oxide and multi-carbon nanotubes after drying;
[0022] 3) Add the pretreated mixture of step 2) into 8wt% carboxymethyl chitosan Schiff base derivative solution for ultrasonic dispersion, heat up to 40°C for reaction, perform ultrasonic dispersion after the reaction, and filter and dry. The mass ratio of graphene oxide, multi-carbon nanotubes and carboxymethyl chitosan Schiff base derivatives is 7:6:13.
Embodiment 2
[0024] The preparation method of flame retardant comprises the following steps:
[0025] 1) adding graphene oxide to 10wt% citric acid solution for soaking for 6 hours, and filtering to obtain acid-treated graphene oxide;
[0026] 2) Add multi-carbon nanotubes to the mixed acid solution of 20wt% dilute nitric acid and 10wt% dilute sulfuric acid, then add the acid-treated graphene oxide of step 1) for ultrasonic dispersion, filter and wash until the filtrate is neutral , to obtain a mixture of pretreated graphene oxide and multi-carbon nanotubes after drying;
[0027] 3) Add the pretreated mixture of step 2) into 4wt% carboxymethyl chitosan Schiff base derivative solution for ultrasonic dispersion, heat up to 60°C for reaction, perform ultrasonic dispersion after the reaction, and filter and dry. The mass ratio of graphene oxide, multi-carbon nanotubes and carboxymethyl chitosan Schiff base derivatives is 11:4:10.
Embodiment 3
[0029] A fire-retardant coating for floors, comprising the following components in parts by weight:
[0030] 50 parts of acrylic emulsion, 28 parts of pure acrylic emulsion, 6 parts of vermiculite powder, 7 parts of superfine dolomite, 12 parts of flame retardant of Example 1, 0.6 part of sodium hexametaphosphate wetting agent, 0.5 part of water-based acrylate copolymer And 10 parts of titanium dioxide, 10 parts of montmorillonite.
PUM
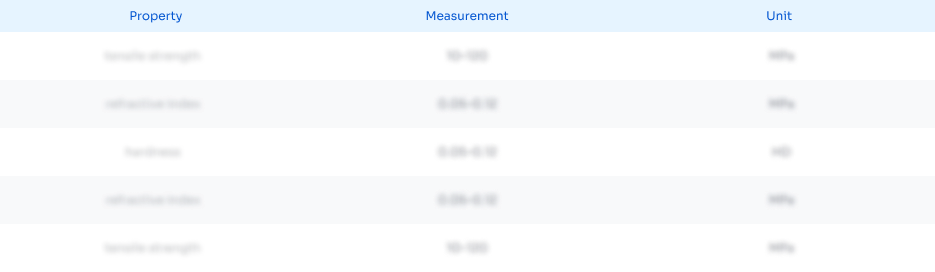
Abstract
Description
Claims
Application Information

- R&D Engineer
- R&D Manager
- IP Professional
- Industry Leading Data Capabilities
- Powerful AI technology
- Patent DNA Extraction
Browse by: Latest US Patents, China's latest patents, Technical Efficacy Thesaurus, Application Domain, Technology Topic, Popular Technical Reports.
© 2024 PatSnap. All rights reserved.Legal|Privacy policy|Modern Slavery Act Transparency Statement|Sitemap|About US| Contact US: help@patsnap.com