Fault diagnosis method for inner ring and outer ring of bearing of axial plunger pump
A technology for axial piston pumps and bearing inner rings, applied in the field of fault diagnosis of axial piston pump bearings, can solve problems such as vibration signal noise pollution, impact component interference, and ineffective effects
- Summary
- Abstract
- Description
- Claims
- Application Information
AI Technical Summary
Problems solved by technology
Method used
Image
Examples
Embodiment example 1
[0102] Example Case 1: Fault Diagnosis of Outer Ring of Axial Piston Pump Bearing
[0103] Taking the fault signal of an axial piston pump in a real hydraulic transmission system, the outer ring of the bearing of the axial piston pump used in the experiment has a fault. The bearing is a specially customized bearing, and the radial load is F r =4900N, lubricating oil viscosity coefficient α=2.3×10 3 , the dynamic viscosity η of lubricating oil at atmospheric pressure 0 =0.02Pa / s, original clearance G r =8μm, the number of rolling elements is Z=17, and the diameter of rolling elements is d r =9mm, the pitch circle diameter of the bearing is d p =49.15mm, geometric dimensions such as figure 2 shown. The rated working pressure of the axial piston pump is 35Mpa, and the number of plungers is n p = 9, the working axis rotation frequency is f shaft = 16.67Hz, the fault characteristic frequency value of the outer ring of the bearing RPFO = 115.75Hz, the natural interference fr...
Embodiment example 2
[0111] Implementation Case 2: Fault Diagnosis of Axial Piston Pump Bearing Inner Ring
[0112] Take the fault signal of an axial piston pump in a real hydraulic transmission system. The inner ring of the axial piston pump bearing used in the experiment has a fault. The bearing is a specially customized bearing with a radial load of F r =4900N, lubricating oil viscosity coefficient α=2.3×10 3 , the dynamic viscosity η of lubricating oil at atmospheric pressure 0 =0.02Pa / s, original clearance G r =8μm, the number of rolling elements is Z=17, the rolling element diameter is d=9mm, the pitch circle diameter of the bearing is D=49.15mm, the geometric dimensions are as follows figure 2 shown. The rated working pressure of the axial piston pump is 35Mpa, and the number of plungers is n p = 9, the working axis rotation frequency is f shaft = 21.67Hz, the fault characteristic frequency value of the outer ring of the bearing RPFI = 217.92Hz, the natural interference frequency f d...
PUM
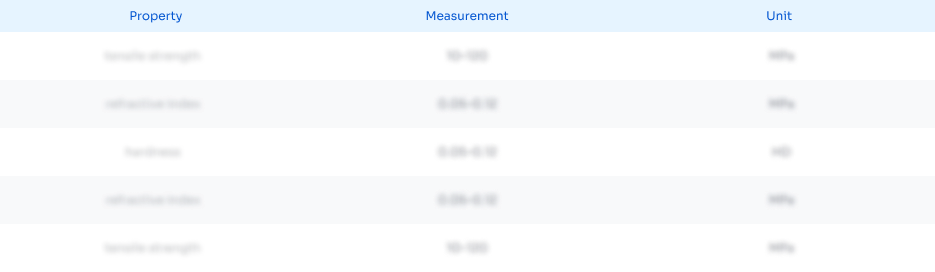
Abstract
Description
Claims
Application Information

- R&D
- Intellectual Property
- Life Sciences
- Materials
- Tech Scout
- Unparalleled Data Quality
- Higher Quality Content
- 60% Fewer Hallucinations
Browse by: Latest US Patents, China's latest patents, Technical Efficacy Thesaurus, Application Domain, Technology Topic, Popular Technical Reports.
© 2025 PatSnap. All rights reserved.Legal|Privacy policy|Modern Slavery Act Transparency Statement|Sitemap|About US| Contact US: help@patsnap.com