Online monitoring method for liquidity of internal resin of fiber reinforced resin matrix composite material
A fiber reinforced resin, resin fluidity technology, applied in the field of composite fluidity testing and analysis, can solve the problems that the fluidity cannot be monitored online, and the resin fluidity cannot be characterized and measured, and achieves low cost, small size, and reduced porosity. Effect
- Summary
- Abstract
- Description
- Claims
- Application Information
AI Technical Summary
Problems solved by technology
Method used
Image
Examples
example 2
[0082] The difference between this example and Example 1 is that the heating rate in the temperature process is different. In this example, the heating rate is changed to 1°C / min and 5°C / min, and the rest are the same as the above-mentioned Example 1.
[0083] 1. The results of online monitoring of resin fluidity in composite materials are as follows: Image 6 As shown, it can be found that the effective resin flow time is 70min in the 1°C / min process, 19min in the 3°C / min process, and 18min in the 5°C / min process . It can be judged that there are significant differences in the effective resin flow time under different temperature processes.
[0084] 2. Cut a sample with a size of 20*5mm from the center of the composite material sample cured at three different heating rates, then observe the pore distribution under a microscope, and calculate the composite material sample according to the ratio of the pore area to the cross-section of the sample Porosity in . The porosity o...
example 3
[0086] The difference between this example and examples 1 and 2 is that the resin fluidity in the cross-laminated composite material is monitored online, and the optical fiber is placed along the fiber direction of any one of the two adjacent layers, and the fiber and optical fiber of this layer form half of the example 1. The sensing structure, such as Figure 8 shown. The capillary force in this structure still obeys the high-low-high step distribution, and the resin fluidity in the cross-laminated composite can still be monitored online.
example 4
[0088] The difference between this example and examples 1, 2 and 3 is that the sensor is used to monitor and control the flow state of resin during high-pressure molding of composite materials.
PUM
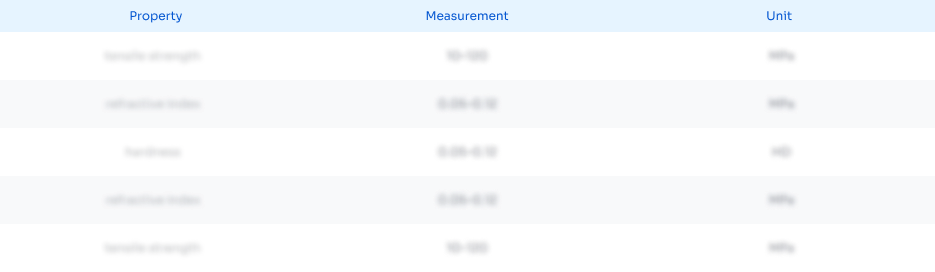
Abstract
Description
Claims
Application Information

- Generate Ideas
- Intellectual Property
- Life Sciences
- Materials
- Tech Scout
- Unparalleled Data Quality
- Higher Quality Content
- 60% Fewer Hallucinations
Browse by: Latest US Patents, China's latest patents, Technical Efficacy Thesaurus, Application Domain, Technology Topic, Popular Technical Reports.
© 2025 PatSnap. All rights reserved.Legal|Privacy policy|Modern Slavery Act Transparency Statement|Sitemap|About US| Contact US: help@patsnap.com