A method for efficiently recovering silicon metal in silicon slag
A technology of silicon metal and silicon slag, which is applied in the field of silicon metal in the efficient recovery of silicon slag, can solve the problem of high impurity elements and achieve the effect of improving the recycling rate
- Summary
- Abstract
- Description
- Claims
- Application Information
AI Technical Summary
Problems solved by technology
Method used
Examples
Embodiment 1
[0025] Crumble the silicon slag with a silicon content of 65% as a raw material and pass it through a 10-mesh sieve, then add a 20mol / L sodium hydroxide solution with a molar concentration of 5% by mass of the silicon slag, stir evenly, and stand at a temperature of 50°C for 72 hours to obtain material a ; 30 parts by weight of CaO and 40 parts of Al are added to material a by 0.5 times of the quality of material a 2 o 3 , 30 parts of SiO 2 and 50 parts of Na 2 O to form a slagging agent, stir evenly to obtain material b; uniformly raise the temperature of material b to 1550°C at a heating rate of 15°C / min, and keep it warm for 2 hours until the silicon slag and metal silicon are completely separated. Metal silicon has good fluidity and small specific gravity Floating above, silicon and silicon slag are separated, and the silicon melt is poured to obtain silicon metal with a purity of 99.3% and a Fe content of 0.7%, an Al content of 0.08%, and a Ca content of 0.01%, and the ...
Embodiment 2
[0027] Crumble silicon slag with a silicon content of 63% as a raw material and pass through a 20-mesh sieve, then add a 18mol / L sodium hydroxide solution with a molar concentration of 10% by mass of the silicon slag, stir evenly, and stand at a temperature of 35°C for 48 hours to obtain material a ; Add material a quality 1.5 times by the CaO of 35 parts by weight, the Al of 45 parts in material a 2 o 3 , 35 parts of SiO 2 and 55 parts of Na 2 O is a slag-forming agent, stirred evenly to obtain material b; uniformly raise the temperature of material b to 1750°C at a heating rate of 25°C / min, and keep it warm for 1 hour until the silicon slag and metal silicon are completely separated. Floating above, silicon and silicon slag are separated and the silicon melt is poured to obtain silicon metal with a purity of 99.2% and a Fe content of 0.6%, an Al content of 0.06%, and a Ca content of 0.009%, and the rest are inevitable impurities.
Embodiment 3
[0029] Crumble silicon slag with a silicon content of 68% as a raw material and pass through a 20-mesh sieve, then add a 19mol / L sodium hydroxide solution with a molar concentration of 8% by mass of the silicon slag, stir evenly, and stand at a temperature of 40°C for 50 hours to obtain material a ; Add material a quality 1.0 times by the CaO of 45 parts by weight, the Al of 55 parts in material a 2 o 3 , 40 parts of SiO 2 and 65 parts of Na 2 O constitutes a slagging agent, stir evenly to obtain material b; uniformly raise the temperature of material b to 1750°C at a heating rate of 30°C / min, and keep it warm for 2 hours until the silicon slag and metal silicon are completely separated. Floating above, silicon and silicon slag are separated, and the silicon melt is poured to obtain silicon metal with a purity of 99.5% and a Fe content of 0.5%, an Al content of 0.05%, and a Ca content of 0.008%, and the rest are unavoidable impurities.
PUM
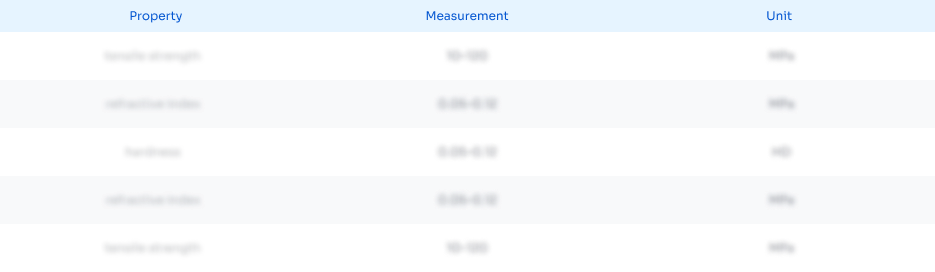
Abstract
Description
Claims
Application Information

- Generate Ideas
- Intellectual Property
- Life Sciences
- Materials
- Tech Scout
- Unparalleled Data Quality
- Higher Quality Content
- 60% Fewer Hallucinations
Browse by: Latest US Patents, China's latest patents, Technical Efficacy Thesaurus, Application Domain, Technology Topic, Popular Technical Reports.
© 2025 PatSnap. All rights reserved.Legal|Privacy policy|Modern Slavery Act Transparency Statement|Sitemap|About US| Contact US: help@patsnap.com