High-strength polyester POY oily agent and preparation method thereof
A technology of high-strength polyester and oil agent, applied in the direction of wear-resistant fibers, fiber types, textiles and papermaking, etc., can solve the problems of increased dynamic friction coefficient, reduced fiber-fiber static friction coefficient, unfavorable stretching, etc., to achieve unwinding Good, improve heat resistance, increase strength effect
- Summary
- Abstract
- Description
- Claims
- Application Information
AI Technical Summary
Problems solved by technology
Method used
Image
Examples
Embodiment 1
[0046] Embodiment 1: the preparation of Chinese tallow tree oil modified alkyd resin
[0047] Put 250 kg of tallow tree oil and 100 kg of glycerin into the reactor, raise the temperature to 120°C, add 1.5 kg of lithium hydroxide under stirring, then raise the temperature to 220°C, stir for 1 hour, add 200 kg of phthalic anhydride, 100 kg of butyl acetate kg, 50 kg of acetone. Reflux for 3 hours, then lower to 25°C for later use.
[0048] The technical indicators achieved are as follows:
[0049] Appearance: clear and transparent, without mechanical impurities;
[0050] Acid value: ≤15 mg LiOH / g;
[0051] Color: ≤10 (iron-cobalt method);
[0052] Viscosity: 8-10 seconds (25°C);
[0053] Solid content: 60±2%;
[0054] Fineness: ≤10 microns.
Embodiment 2
[0055] Embodiment 2: the preparation of Chinese tallow tree oil modified alkyd resin
[0056]Put 250 kg of tallow tree oil and 100 kg of glycerin into the reaction kettle, raise the temperature to 150°C, add 1.5 kg of lithium hydroxide under stirring, then raise the temperature to 150°C, stir and react for 3 hours, add 200 kg of phthalic anhydride, 100 kg of butyl acetate kg, 50 kg of acetone. Reflux reaction for 1 hour, lower to 25°C for later use.
[0057] The technical indicators achieved are as follows:
[0058] Appearance: clear and transparent, without mechanical impurities;
[0059] Acid value: ≤15 mg LiOH / g;
[0060] Color: ≤10 (iron-cobalt method);
[0061] Viscosity: 8-10 seconds (25°C);
[0062] Solid content: 60±2%;
[0063] Fineness: ≤10 microns.
Embodiment 3
[0064] Embodiment 3: the preparation of Chinese tallow tree oil modified alkyd resin
[0065] Put 250 kg of tallow tree oil and 100 kg of glycerin into the reactor, raise the temperature to 120°C, add 5 kg of lithium hydroxide under stirring, then raise the temperature to 220°C, stir for 1 hour, add 100 kg of phthalic anhydride, 50 kg of butyl acetate kg, 10 kg of acetone. Reflux for 3 hours, then lower to 25°C for later use.
[0066] The technical indicators achieved are as follows:
[0067] Appearance: clear and transparent, without mechanical impurities;
[0068] Acid value: ≤15 mg LiOH / g;
[0069] Color: ≤10 (iron-cobalt method);
[0070] Viscosity: 8-10 seconds (25°C);
[0071] Solid content: 60±2%;
[0072] Fineness: ≤10 microns.
PUM
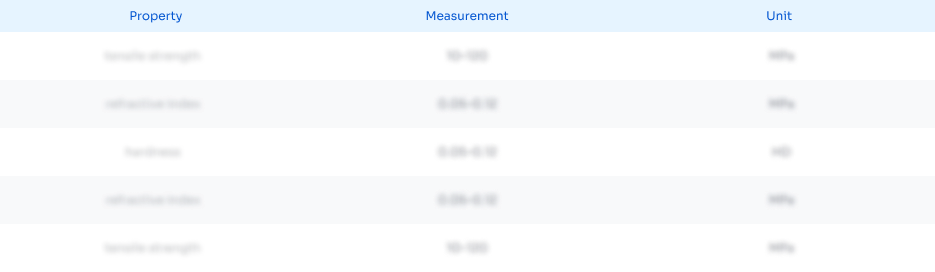
Abstract
Description
Claims
Application Information

- R&D
- Intellectual Property
- Life Sciences
- Materials
- Tech Scout
- Unparalleled Data Quality
- Higher Quality Content
- 60% Fewer Hallucinations
Browse by: Latest US Patents, China's latest patents, Technical Efficacy Thesaurus, Application Domain, Technology Topic, Popular Technical Reports.
© 2025 PatSnap. All rights reserved.Legal|Privacy policy|Modern Slavery Act Transparency Statement|Sitemap|About US| Contact US: help@patsnap.com