Method based on high-silicon high-phosphorus molten iron converter low slag material consumption to melt low-phosphorus steel
A low-phosphorus steel and molten iron technology, which is applied in the direction of manufacturing converters and improving process efficiency, can solve the problems of low metal yield, increased steelmaking costs, sticking guns and splashing, etc., and achieves high metal yield. , the production rhythm is fast, the effect is easy to operate
- Summary
- Abstract
- Description
- Claims
- Application Information
AI Technical Summary
Problems solved by technology
Method used
Image
Examples
Embodiment 1
[0027] 105t of molten iron is added to 32t of scrap steel. The Si content of the molten iron is 0.6591%, the P content of the molten iron is 0.179%, and the temperature of the molten iron is 1373°C. At the same time, there is about 5 tons of final slag left in this furnace, and 29.4kg / t of lime, 18kg / t of dolomite and 12kg / t of tailings are added at the same time as the blowing is started, and 10kg / t of lime is added before blowing 30% of oxygen. A total of slag 69.4kg / t. Endpoint P was 0.0129%.
[0028] Mainly follow the steps below:
[0029] (1) Low-phosphorus steel was smelted by leaving slag in the previous furnace + single slag method, leaving about 5 tons of high-oxidizing slag in the furnace after tapping;
[0030] (2) The conditions of molten iron entering the furnace are controlled at 0.55%≤Si≤0.8%, 0.18%≤P≤0.22%;
[0031] (3) The addition of auxiliary materials, 29.4kg / t of lime, 18kg / t of dolomite, 12kg / t of tailings are added at the same time as the blowing is ...
Embodiment 2
[0037] The molten iron is 104.5t, and 32t of steel scrap is added. Compared with Example 1, this example differs in the amount of smelting slag added, the tapping temperature, and the carbon content at the end point. The Si content of the molten iron is 0.59%, the end point P content is 0.1879%, the temperature of the molten iron is 1360°C, and the operation is carried out by the method of leaving slag + single slag. At the same time, about 5t of the final slag of the previous furnace is left in this furnace, and 16kg / t of lime and 16.6kg / t of dolomite are added at the same time as the blowing is started. Mine is 2kg / t, the end point C is 0.09%, and the end point P is 0.012%. A total of 69.2kg / t slag.
Embodiment 3
[0039] The molten iron is 104.66t, and 31t of steel scrap is added. Compared with Example 1, this example differs in the amount of smelting slag added, the tapping temperature, and the carbon content at the end point. The Si content of the molten iron is 0.5788%, the end-point P content is 0.170%, the temperature of the molten iron is 1360°C, and the operation is carried out by the method of leaving slag + single slag. At the same time, there is about 5 tons of final slag left in this furnace, and 33kg / t of lime, 11.8kg / t of dolomite, and 12kg / t of tailings are added at the same time as the blowing is started; Mine is 8kg / t, the end point C is 0.09%, and the end point P is 0.0119%. A total of 69.8g / t of slag.
PUM
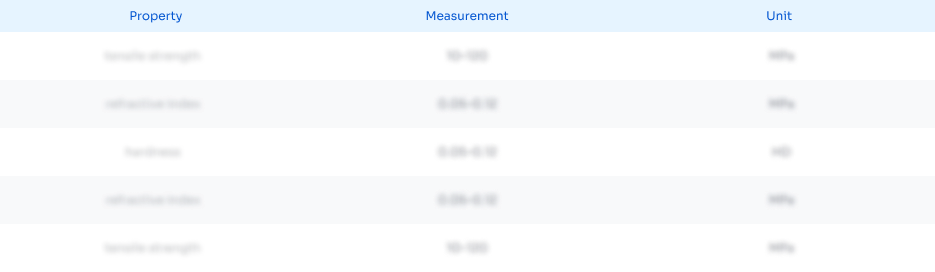
Abstract
Description
Claims
Application Information

- R&D
- Intellectual Property
- Life Sciences
- Materials
- Tech Scout
- Unparalleled Data Quality
- Higher Quality Content
- 60% Fewer Hallucinations
Browse by: Latest US Patents, China's latest patents, Technical Efficacy Thesaurus, Application Domain, Technology Topic, Popular Technical Reports.
© 2025 PatSnap. All rights reserved.Legal|Privacy policy|Modern Slavery Act Transparency Statement|Sitemap|About US| Contact US: help@patsnap.com