Production method of lost foam casting anode steel claw head and anode steel claw head lost module
A technology of lost foam casting and anode steel claw, which is applied in casting molding equipment, casting molds, casting mold components, etc., can solve the problems of increased pressure drop and power loss, easy to be corroded, oxidized, and high production and maintenance costs. The effect of improving grain morphology, improving corrosion resistance and oxidation resistance, and reducing production and maintenance costs
- Summary
- Abstract
- Description
- Claims
- Application Information
AI Technical Summary
Problems solved by technology
Method used
Image
Examples
Embodiment 1
[0038] Such as Figure 1-3 As shown, the present invention provides a kind of production method of lost foam casting anode steel claw head, comprising:
[0039] Step 1, preparing molten steel, the content of chromium in the molten steel is 3%, the content of manganese is 0.6%, the content of carbon is 0.45%, the content of silicon is 0.4%, the content of molybdenum is 0.2%, the content of sulfur is less than 0.04%, and the content of phosphorus is less than 0.04% %, the balance is Fe, and the molten steel is made by directly melting low-carbon steel and alloy materials according to the formula quantity;
[0040] Step 2: Using the lost foam casting process, pour molten steel into the lost die set of the anode steel claw head, cool and form it, and the finished product is obtained.
[0041] Wherein said anode steel claw head disappearing module includes, claw head white mold 1, which is a vertically arranged cylindrical structure, and the opposite sides near the top of the uppe...
Embodiment 2
[0044] The present invention provides a kind of production method of lost foam casting anode steel claw head, comprising:
[0045] Step 1, preparing molten steel, the content of chromium in the molten steel is 4.5%, the content of manganese is 0.9%, the content of carbon is 0.6%, the content of silicon is 0.6%, the content of molybdenum is 0.25%, the content of sulfur is less than 0.04%, and the content of phosphorus is less than 0.04% %, the balance is Fe, and the molten steel is made by directly melting low-carbon steel and alloy materials according to the formula quantity;
[0046] Step 2: Using the lost foam casting process, pour molten steel into the lost die set of the anode steel claw head, cool and form it, and the finished product is obtained. All the other operating conditions are the same as in Example 1.
[0047] After the prepared anode steel claw head was welded to the anode steel claw beam, it was used for performance testing in actual aluminum production, and ...
Embodiment 3
[0049] The present invention provides a kind of production method of lost foam casting anode steel claw head, comprising:
[0050] Step 1, preparing molten steel, the content of chromium in the molten steel is 6%, the content of manganese is 1.2%, the content of carbon is 0.8%, the content of silicon is 0.8%, the content of molybdenum is 0.3%, the content of sulfur is less than 0.04%, and the content of phosphorus is less than 0.04% %, the balance is Fe, and the molten steel is made by directly melting low-carbon steel and alloy materials according to the formula quantity;
[0051] Step 2: Using the lost foam casting process, pour molten steel into the lost die set of the anode steel claw head, cool and form it, and the finished product is obtained. All the other operating conditions are the same as in Example 1.
[0052] The prepared anodized steel claw head was welded to the anode steel claw beam, and then used for performance testing in actual aluminum production. The aver...
PUM
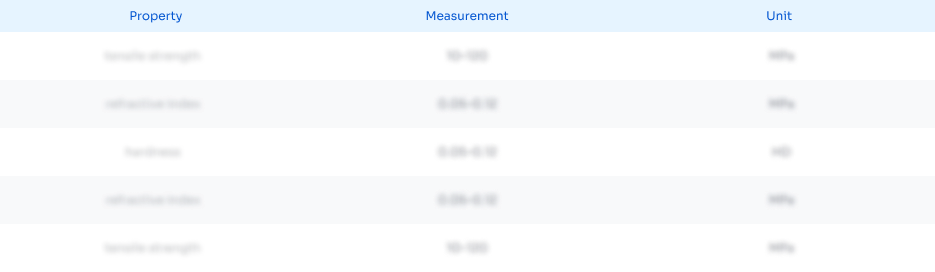
Abstract
Description
Claims
Application Information

- Generate Ideas
- Intellectual Property
- Life Sciences
- Materials
- Tech Scout
- Unparalleled Data Quality
- Higher Quality Content
- 60% Fewer Hallucinations
Browse by: Latest US Patents, China's latest patents, Technical Efficacy Thesaurus, Application Domain, Technology Topic, Popular Technical Reports.
© 2025 PatSnap. All rights reserved.Legal|Privacy policy|Modern Slavery Act Transparency Statement|Sitemap|About US| Contact US: help@patsnap.com