Aluminum alloy forced sizing device and aluminum alloy heat treatment method
A heat treatment method and aluminum alloy profile technology, which is applied in the field of aluminum alloy processing, can solve problems such as bending and deformation of aluminum alloy heat treatment, and achieve the effects of good straightness and deformation prevention
- Summary
- Abstract
- Description
- Claims
- Application Information
AI Technical Summary
Problems solved by technology
Method used
Image
Examples
Embodiment 1
[0047] This embodiment provides a 2026 aluminum alloy product, which is obtained by the following mandatory heat treatment method:
[0048] (1) Extrusion: Heat the aluminum alloy cast rod in a power frequency furnace at a heating temperature of 360°C, put the heated cast rod into an extrusion cylinder for extrusion treatment to obtain an extruded profile, and the exit speed of the extruded profile is 1.5m / min, the outlet temperature is 365°C.
[0049] (2) Quenching: Place the extruded profile in the prefabricated aluminum alloy forced shaping device 100, and enter the horizontal quenching furnace with the feeding basket for solid solution and quenching. The solid solution temperature is 495°C, the holding time is 120min, and quenched The transfer time is 15s, and the quenched profile is obtained.
[0050] The distance between the two single-piece fixtures 120 of the aluminum alloy forced shaping device 100 used in the quenching process is 3m, and a total of 6 single-piece fi...
Embodiment 2
[0055] This embodiment provides a 7150 aluminum alloy product, which is obtained by the following heat treatment method for forced shaping:
[0056] (1) Extrusion: Heat the aluminum alloy cast rod in a power frequency furnace at a heating temperature of 350°C, put the heated cast rod into an extrusion cylinder for extrusion treatment to obtain an extruded profile, and the exit speed of the extruded profile is 1.2m / min, the outlet temperature is 360°C.
[0057] (2) Quenching: the extruded profile is placed in the prefabricated aluminum alloy forced shaping device 100, and enters the horizontal quenching furnace with the feeding basket for solid solution and quenching. The solid solution temperature is 477 ° C, and the holding time is 130 minutes. Quenched profiles.
[0058] (3) Stretching and bending: the quenched profile is stretched within 6 hours, the stretch rate is controlled at 2.0%, and then bent. The bending process is completed with a special mold and an insert to ob...
Embodiment 3
[0063] This embodiment provides a 7055 aluminum alloy product, which is obtained by the following heat treatment method for forced shaping:
[0064] (1) Extrusion: Heat the aluminum alloy cast rod in a power frequency furnace at a heating temperature of 380°C, put the heated cast rod into an extrusion cylinder for extrusion treatment to obtain an extruded profile, and the exit speed of the extruded profile is 0.8m / min, the outlet temperature is 400°C.
[0065] (2) Quenching: Place the extruded profile in the prefabricated aluminum alloy forced shaping device 100, and enter the horizontal quenching furnace with the feeding basket for solid solution and quenching. The solid solution temperature is 477°C, and the holding time is 160min. Quenched profiles.
[0066] The distance between the two single-piece fixtures 120 of the aluminum alloy forced shaping device 100 used in the quenching process is 3m, and a total of 6 single-piece fixtures 120 are provided.
[0067] (3) Stretc...
PUM
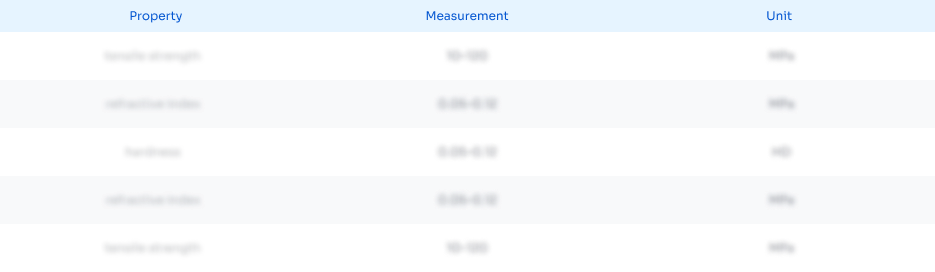
Abstract
Description
Claims
Application Information

- R&D Engineer
- R&D Manager
- IP Professional
- Industry Leading Data Capabilities
- Powerful AI technology
- Patent DNA Extraction
Browse by: Latest US Patents, China's latest patents, Technical Efficacy Thesaurus, Application Domain, Technology Topic, Popular Technical Reports.
© 2024 PatSnap. All rights reserved.Legal|Privacy policy|Modern Slavery Act Transparency Statement|Sitemap|About US| Contact US: help@patsnap.com