Autoclaved aerated concrete plate and molding process thereof
An autoclaved aerated concrete technology, applied in the field of building materials, can solve the problems of rough surface of autoclaved aerated concrete slabs, affecting the aesthetics of partition boards, etc., and achieve the effects of superior stability, wide usability, and thermal insulation surface.
- Summary
- Abstract
- Description
- Claims
- Application Information
AI Technical Summary
Problems solved by technology
Method used
Examples
Embodiment 1
[0046] A preparation method of a powder filler, comprising the steps of:
[0047] (1) Ingredients: Weigh 70g of power furnace dust removal, 5g of activated alumina, 20g of cement clinker powder, 10g of fluorspar powder and 0.3g of sodium dipolyphosphate;
[0048] (2) Drying: Dry 70g of power furnace dust removal at a high temperature of 600°C for 1 hour;
[0049] (3) Calcination: Calcining 10g of fluorspar powder in a tubular heating furnace at a temperature of 150°C for 2 hours;
[0050] (4) Mixing: Throw 70g of dried power furnace ash into the mixing mixer, and add 5g of activated alumina, 20g of cement clinker powder, 10g of fluorspar powder and 0.3g of sodium dipolyphosphate in sequence for mixing After stirring for 30min, the material was discharged.
Embodiment 2
[0052] A preparation method of a powder filler, comprising the steps of:
[0053] (1) Ingredients: Weigh 75g of power furnace dust removal, 5g of activated alumina, 23g of cement clinker powder, 10g of fluorspar powder and 0.3g of sodium tripolyphosphate;
[0054] (2) Drying: Dry 75g of power furnace dust removal at a high temperature of 600°C for 1 hour;
[0055] (3) Calcination: Calcining 10g of fluorspar powder in a tubular heating furnace at a temperature of 150°C for 2 hours;
[0056] (4) Mixing: Throw 75g of the dried power furnace ash into the mixing mixer, and add 5g of activated alumina, 23g of cement clinker powder, 10g of fluorspar powder and 0.3g of sodium tripolyphosphate in sequence for mixing After stirring for 30min, the material was discharged.
Embodiment 3
[0058] A preparation method of a powder filler, comprising the steps of:
[0059] (1) Ingredients: Weigh 80g of power furnace dust removal, 5g of activated alumina, 25g of cement clinker powder, 12g of fluorspar powder and 0.4g of sodium dipolyphosphate;
[0060] (2) Drying: Dry 80g of power furnace dust removal at a high temperature of 600°C for 1 hour;
[0061] (3) Calcination: Calcining 12g of fluorspar powder in a tubular heating furnace at a temperature of 150°C for 2 hours;
[0062] (4) Mixing: Throw 80g of dried power furnace dust into the mixing mixer, and add 5g of activated alumina, 25g of cement clinker powder, 12g of fluorspar powder and 0.4g of sodium dipolyphosphate in sequence for mixing After stirring for 30min, the material was discharged.
PUM
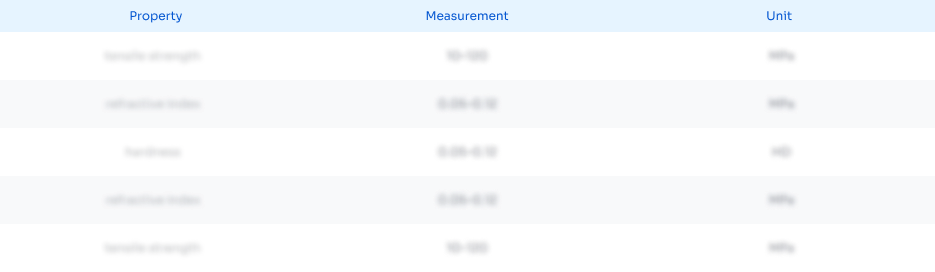
Abstract
Description
Claims
Application Information

- R&D
- Intellectual Property
- Life Sciences
- Materials
- Tech Scout
- Unparalleled Data Quality
- Higher Quality Content
- 60% Fewer Hallucinations
Browse by: Latest US Patents, China's latest patents, Technical Efficacy Thesaurus, Application Domain, Technology Topic, Popular Technical Reports.
© 2025 PatSnap. All rights reserved.Legal|Privacy policy|Modern Slavery Act Transparency Statement|Sitemap|About US| Contact US: help@patsnap.com