Sulfur-loaded heat regeneration method of active carbon mercury removal adsorbing agent
A technology of activated carbon and adsorbent, which is applied in the field of sulfur-loaded heat regeneration, can solve the problem that the activated carbon demercury adsorbent cannot be reused, achieve strong mercury adsorption performance and cycle regeneration characteristics, reduce industrial pollution, and simplify the production process.
- Summary
- Abstract
- Description
- Claims
- Application Information
AI Technical Summary
Problems solved by technology
Method used
Image
Examples
Embodiment 1
[0043] Weigh 100 mg of sample, crush and grind the activated carbon mercury removal adsorbent with an agate mortar, use a 160-mesh standard sieve to obtain a 160-mesh particle size; then mix it with 100 mg of sulfur and put it into a crucible; put the crucible into a quartz In the reaction tube, the quartz reaction tube is placed in the effective heating constant temperature zone of the tube furnace, and the high-purity N 2 Under the protection of the atmosphere, the tube furnace was raised from room temperature to 500 °C at a rate of 15 °C / min; the heating was stopped after the constant temperature was maintained for 1 hour, and it was taken out after cooling to room temperature to prepare the sulfur-loaded heat-regenerating activated carbon adsorbent for mercury removal. Process such as figure 1 shown.
[0044] Mercury removal performance test of the regenerated activated carbon adsorbent for mercury removal: the initial mercury removal efficiency was about 78.17%, and rema...
Embodiment 2
[0046] Weigh 100 mg of sample, crush and grind the activated carbon mercury removal adsorbent with an agate mortar, use a 250-mesh standard sieve to obtain a 250-mesh particle size; then mix it with 100 mg of sulfur and put it into a crucible; put the crucible into a quartz In the reaction tube, the quartz reaction tube was placed in the effective heating constant temperature zone of the tube furnace. Under the protection of the high-purity He atmosphere with a flow rate of 0.015m / s, the tube furnace heated up from the chamber at a rate of 10°C / min. The temperature was raised to 600°C; the heating was stopped after the constant temperature was kept for 1 hour, and it was taken out after cooling to room temperature to obtain a sulfur-loaded thermally regenerated activated carbon adsorbent for mercury removal.
[0047] Mercury removal performance test of the regenerated activated carbon adsorbent for mercury removal: the initial mercury removal efficiency was about 98.14%, and it...
Embodiment 3
[0049] Weigh 100 mg of sample, crush and grind the activated carbon mercury removal adsorbent with an agate mortar, use a 200-mesh standard sieve to obtain a 200-mesh particle size; then mix it with 100 mg of sulfur and put it into a crucible; put the crucible into a quartz In the reaction tube, the quartz reaction tube is placed in the effective heating constant temperature zone of the tube furnace. Under the protection of the high-purity Ne atmosphere with a flow rate of 0.02m / s, the tube furnace heats up from the chamber at a rate of 20°C / min. The temperature was raised to 700°C; the heating was stopped after the constant temperature was kept for 1 hour, and it was taken out after cooling to room temperature to obtain a sulfur-loaded thermally regenerated activated carbon adsorbent for mercury removal.
[0050] Mercury removal performance test of the regenerated activated carbon adsorbent for mercury removal: the initial mercury removal efficiency was about 92.38%, and it re...
PUM
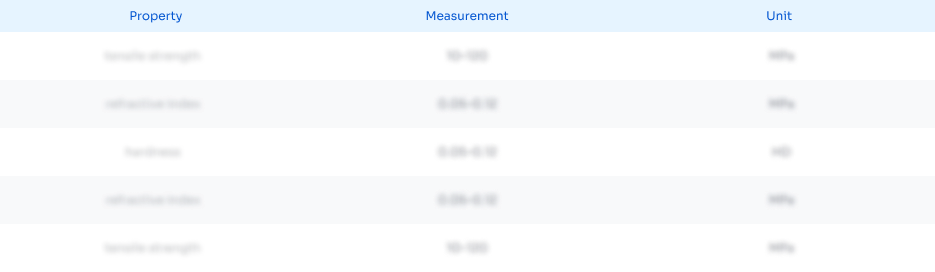
Abstract
Description
Claims
Application Information

- R&D Engineer
- R&D Manager
- IP Professional
- Industry Leading Data Capabilities
- Powerful AI technology
- Patent DNA Extraction
Browse by: Latest US Patents, China's latest patents, Technical Efficacy Thesaurus, Application Domain, Technology Topic, Popular Technical Reports.
© 2024 PatSnap. All rights reserved.Legal|Privacy policy|Modern Slavery Act Transparency Statement|Sitemap|About US| Contact US: help@patsnap.com