Thermochromic aluminum silicate glass and preparation method thereof
An aluminosilicate glass and thermochromic technology, which is applied in the field of special glass manufacturing and color-changing glass production to achieve the effects of high elastic modulus, fast discoloration response time and simple production process
- Summary
- Abstract
- Description
- Claims
- Application Information
AI Technical Summary
Problems solved by technology
Method used
Examples
Embodiment 1
[0016] (1) SiO by weight percentage 2 57%, Al 2 o 3 15%, B 2 o 3 4%, K 2 O 7.5%, MgO 2%, CaO 0.5%, Na 2 O14%, VO 2 0.8% for batching;
[0017] (2) Put the prepared above-mentioned raw materials into a ball mill for mixing and grinding, and the ball milling time is 60 min to obtain a uniform mixture;
[0018] (3) Melt the ground mixture in a furnace, raise the temperature to 1000°C at a rate of 10°C / min, then raise the temperature to 1300°C at a rate of 5°C / min, control the melting temperature to 1300°C, and keep it warm for 5 hours. Obtain clarified and homogenized molten glass;
[0019] (4) Quickly pour the molten glass into a stainless steel plate mold to form it, and select the corresponding size abrasive tool according to the amount of batching materials;
[0020] (5) Immediately put the formed glass sample into an annealing furnace, keep it warm at 650°C for 3 hours, and cool the glass sample to room temperature with the furnace to obtain a thermochromic alum...
Embodiment 2
[0022] (1) SiO by weight percentage 2 60%, Al 2 o 3 24%, B 2 o 3 1%, K 2 O 4%, MgO 0.5%, CaO 1%, Na 2 O9.5%,, VO 2 2% for batching;
[0023] (2) Put the prepared above-mentioned raw materials into a ball mill for mixing and grinding, and the ball milling time is 80 min to obtain a uniform mixture;
[0024] (3) Melt the ground mixture in a furnace, raise the temperature to 1000°C at a rate of 8°C / min, then raise the temperature to 1500°C at a rate of 4°C / min, control the melting temperature to 1500°C, and keep it warm for 2 hours. Obtain clarified and homogenized molten glass;
[0025] (4) Quickly pour the molten glass into a stainless steel plate mold to form it, and select the corresponding size abrasive tool according to the amount of batching materials;
[0026] (5) Immediately put the formed glass sample into an annealing furnace, keep it warm at 650°C for 4 hours, and cool the glass sample to room temperature with the furnace to obtain a thermochromic alumino...
Embodiment 3
[0028] (1) SiO by weight percentage 2 66%, Al 2 o 3 20%, B 2 o 3 2%, SiO 2 66%, K 2 O 2%, MgO 4%, CaO 1%, Na 2 O 5%, VO 2 5% for batching;
[0029] (2) Put the prepared above-mentioned raw materials into a ball mill for mixing and grinding, and the ball milling time is 100 min to obtain a uniform mixture;
[0030] (3) Melt the ground mixture in a furnace, raise the temperature to 1000°C at a rate of 8°C / min, then raise the temperature to 1400°C at a rate of 4°C / min, control the melting temperature to 1400°C, and keep it warm for 3 hours. Obtain clarified and homogenized molten glass;
[0031] (4) Quickly pour the molten glass into a stainless steel plate mold to form it, and select the corresponding size abrasive tool according to the amount of batching materials;
[0032] (5) Immediately put the formed glass sample into an annealing furnace, keep it warm at 650°C for 5 hours, and cool the glass sample to room temperature with the furnace to obtain a thermochromi...
PUM
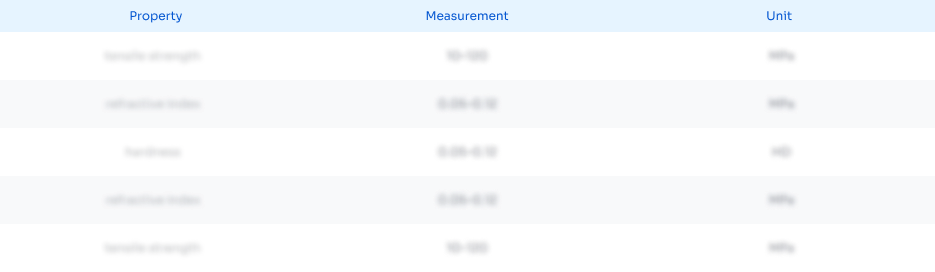
Abstract
Description
Claims
Application Information

- R&D Engineer
- R&D Manager
- IP Professional
- Industry Leading Data Capabilities
- Powerful AI technology
- Patent DNA Extraction
Browse by: Latest US Patents, China's latest patents, Technical Efficacy Thesaurus, Application Domain, Technology Topic, Popular Technical Reports.
© 2024 PatSnap. All rights reserved.Legal|Privacy policy|Modern Slavery Act Transparency Statement|Sitemap|About US| Contact US: help@patsnap.com