Melting device for producing inorganic fibers
A melting device, inorganic fiber technology, applied in the direction of inorganic raw material rayon, furnace, retort furnace, etc., can solve the problems of energy consumption, low furnace lining life, poor heat resistance, etc., to ensure operation and high combustion efficiency. Effect
- Summary
- Abstract
- Description
- Claims
- Application Information
AI Technical Summary
Problems solved by technology
Method used
Image
Examples
Embodiment
[0023] When in use, rocks (such as basalt, diabase, dolomite, etc.) or iron slag are used as the main raw materials and fed into the melting device through the feeding port. Natural gas enters the annular combustion chamber through the fuel pipe network, and at the same time, the combustion-supporting air system sends a large amount of oxygen-enriched air into the combustion chamber. After the combustion control system ignites the burner, it starts to burn and releases a large amount of heat. At high temperature, the material in the melting device gradually becomes molten, and reaches the viscosity and crystallization degree required by the process, flows out through the orifice and enters the next process of centrifugal spinning to make inorganic fibers. The combustion exhaust gas can be discharged into the atmosphere after being strictly purified by the smoke exhaust purification system.
PUM
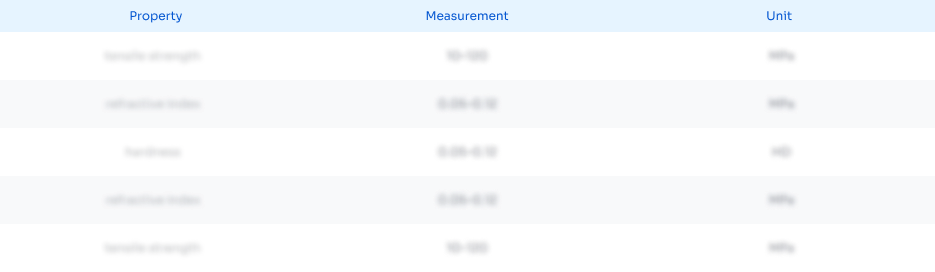
Abstract
Description
Claims
Application Information

- Generate Ideas
- Intellectual Property
- Life Sciences
- Materials
- Tech Scout
- Unparalleled Data Quality
- Higher Quality Content
- 60% Fewer Hallucinations
Browse by: Latest US Patents, China's latest patents, Technical Efficacy Thesaurus, Application Domain, Technology Topic, Popular Technical Reports.
© 2025 PatSnap. All rights reserved.Legal|Privacy policy|Modern Slavery Act Transparency Statement|Sitemap|About US| Contact US: help@patsnap.com