Screen printing ink and manufacturing process thereof
A technology of screen printing ink and process, applied in the field of screen printing ink and its application process, can solve the problems of insufficient ink adhesion, affecting product quality, low printing quality, etc., and achieve the effect of high screen printing efficiency, simple process and convenient operation.
- Summary
- Abstract
- Description
- Claims
- Application Information
AI Technical Summary
Problems solved by technology
Method used
Examples
Embodiment 1
[0020] The invention provides a screen printing ink. The screen printing ink is composed of printing color ink and curing agent, wherein the printing color ink is 100mL, and the curing agent is 3-10mL. The printing ink in this embodiment is champagne gold ink, and the curing agent is 10 mL. The curing agent has the function of hardening the ink. Adding too much will make the surface of the ink too hard. If it is too hard, the ink will become brittle and affect the use. If adding too little, the adhesion of the ink will not be enough. Add 10mL of curing agent to 100mL champagne gold ink , which will not make the ink too brittle, but also achieve the best adhesion effect.
[0021] The curing agent in this example is formed by mixing components such as acrylic baking varnish, isophorone, cyclohexanone and butyl acetate, wherein the acrylic baking varnish is 100mL, isophorone is 40mL, and cyclohexanone is 20mL , 25 mL of butyl acetate. In the screen printing ink in this embodime...
Embodiment 2
[0034]The present invention provides another screen printing ink. The composition of the screen printing ink in this embodiment is basically the same as that in Embodiment 1, the difference lies in that the printing color ink is different and the content of the curing agent is also different. The printing ink in this embodiment is mirror silver ink, and the curing agent is 3mL. The curing agent has the function of hardening the ink. Adding too much will make the surface of the ink too hard. If it is too hard, the ink will become brittle and affect the use. Adding too little will make the adhesion of the ink insufficient. In addition, adding too much curing agent to the mirror silver ink will affect the mirror effect. Therefore, in this embodiment, 3mL of curing agent is added to 100mL of mirror silver ink, which not only achieves a better adhesion effect, but also does not affect the mirror effect.
[0035] The above-mentioned application process of screen printing ink compri...
PUM
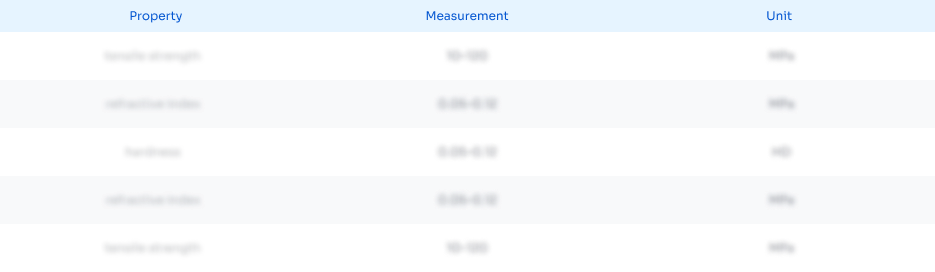
Abstract
Description
Claims
Application Information

- R&D
- Intellectual Property
- Life Sciences
- Materials
- Tech Scout
- Unparalleled Data Quality
- Higher Quality Content
- 60% Fewer Hallucinations
Browse by: Latest US Patents, China's latest patents, Technical Efficacy Thesaurus, Application Domain, Technology Topic, Popular Technical Reports.
© 2025 PatSnap. All rights reserved.Legal|Privacy policy|Modern Slavery Act Transparency Statement|Sitemap|About US| Contact US: help@patsnap.com