Production of bg65mn steel for ball mill grinding rods by electric furnace continuous casting and its preparation method
A technology of ball mill and continuous casting, applied in the direction of electric furnace, furnace, furnace type, etc., can solve the problem of less grinding rods, achieve the effect of improving product quality, reducing energy consumption, and ensuring fluidity
- Summary
- Abstract
- Description
- Claims
- Application Information
AI Technical Summary
Problems solved by technology
Method used
Examples
Embodiment 1
[0016] Electric furnace continuous casting produces BG65Mn steel for ball mill grinding rods, by weight percentage, including the following components: C: 0.64%, Si: 0.20%, Mn: 1.05%, Cr: 0.22%, Alt: 0.020%, and the rest is iron and unavoidable impurities.
[0017] The method for preparing the above-mentioned electric furnace continuous casting to produce ball mill grinding rods with BG65Mn steel:
[0018] Raw materials are pretreated in turn→electric furnace smelting→refining furnace LF→vacuum degassing VD→medium billet continuous casting 235mm×265mm continuous casting slab→walking heating furnace heating→high pressure water descaling→rough rolling mill rolling→continuous rolling unit→ Slow cooling→finishing→flaw detection→inspection to obtain steel,
[0019] In the LF process of the refining furnace, control FeO+MnO≤1% to obtain white slag, which lasts for more than 15 minutes;
[0020] In the vacuum degassing VD process, the vacuum lasts for more than 25 minutes;
[0021...
Embodiment 2
[0023] Electric furnace continuous casting produces BG65Mn steel for ball mill grinding rods, by weight percentage, including the following components: C: 0.67%, Si: 0.35%, Mn: 1.15%, P: 0.020%, S: 0.015%, Cr: 0.28% , Cu: 0.15%, Alt: 0.035%, and the rest are iron and unavoidable impurities.
[0024] The method for preparing the above-mentioned electric furnace continuous casting to produce ball mill grinding rods with BG65Mn steel:
[0025] Raw materials are pretreated in turn→electric furnace smelting→refining furnace LF→vacuum degassing VD→medium billet continuous casting 235mm×265mm continuous casting slab→walking heating furnace heating→high pressure water descaling→rough rolling mill rolling→continuous rolling unit→ Slow cooling→finishing→flaw detection→inspection to obtain steel,
[0026] In the LF process of the refining furnace, control FeO+MnO≤1% to obtain white slag, which lasts for more than 15 minutes;
[0027] In the vacuum degassing VD process, the vacuum lasts...
Embodiment 3
[0030] Electric furnace continuous casting produces BG65Mn steel for ball mill grinding rods, by weight percentage, including the following components: C: 0.65%, Si: 0.30%, Mn: 1.10%, P: 0.015%, S: 0.010%, Cr: 0.26% , Cu: 0.05%, Alt: 0.030%, and the rest are iron and unavoidable impurities.
[0031] The method for preparing the above-mentioned electric furnace continuous casting to produce ball mill grinding rods with BG65Mn steel:
[0032] Raw materials are pretreated in turn→electric furnace smelting→refining furnace LF→vacuum degassing VD→medium billet continuous casting 235mm×265mm continuous casting slab→walking heating furnace heating→high pressure water descaling→rough rolling mill rolling→continuous rolling unit→ Slow cooling→finishing→flaw detection→inspection to obtain steel,
[0033] In the LF process of the refining furnace, control FeO+MnO≤1% to obtain white slag, which lasts for more than 15 minutes;
[0034] In the vacuum degassing VD process, the vacuum lasts...
PUM
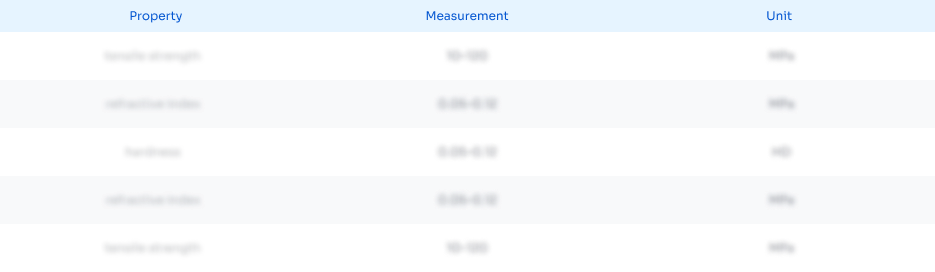
Abstract
Description
Claims
Application Information

- R&D Engineer
- R&D Manager
- IP Professional
- Industry Leading Data Capabilities
- Powerful AI technology
- Patent DNA Extraction
Browse by: Latest US Patents, China's latest patents, Technical Efficacy Thesaurus, Application Domain, Technology Topic, Popular Technical Reports.
© 2024 PatSnap. All rights reserved.Legal|Privacy policy|Modern Slavery Act Transparency Statement|Sitemap|About US| Contact US: help@patsnap.com