Two-phase separation micro-channel heat sink
A micro-channel and phase-separation technology, applied in electrical components, electrical solid devices, circuits, etc., can solve problems such as excessive fluid pressure drop, deterioration of micro-channel heat sink heat dissipation, flow instability, etc., to enhance heat exchange capacity. , Solve the phenomenon of excessive fluid pressure drop and flow instability, and increase the effect of heat exchange area
- Summary
- Abstract
- Description
- Claims
- Application Information
AI Technical Summary
Problems solved by technology
Method used
Image
Examples
Embodiment Construction
[0016] Specific embodiments of the present invention are given below. The specific embodiments are only used to further describe the present invention in detail, and do not limit the protection scope of the claims of this application.
[0017] The invention provides a two-phase separation microchannel heat sink (see Figure 1-4 , Referred to as heat sink), characterized in that the heat sink includes a microchannel array, a bottom plate 5 and a cover plate 6;
[0018] The bottom plate 5 and the cover plate 6 are connected by bonding to form the main structure of the heat sink; the bottom plate 5 is etched with a microchannel array, which is composed of a gas channel 3 and a liquid channel 4, wherein the gas channel 3 and the liquid channel 4 are staggered, and the side walls of the gas channel and the liquid channel are both multi-through-hole structures 9; the cover plate 6 has a gas inlet 1, a liquid inlet 2, a gas outlet 7 and a liquid outlet 8;
[0019] The gas channel 3 has a ...
PUM
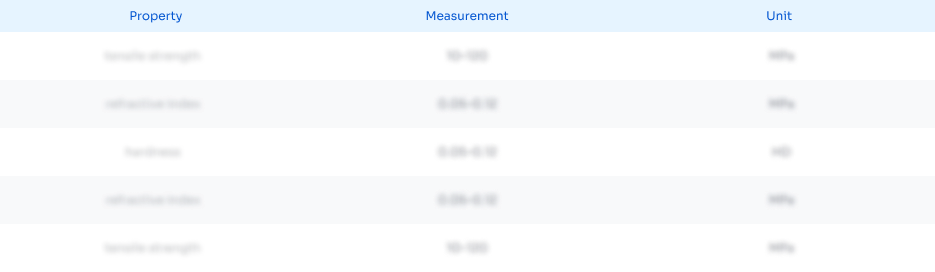
Abstract
Description
Claims
Application Information

- R&D
- Intellectual Property
- Life Sciences
- Materials
- Tech Scout
- Unparalleled Data Quality
- Higher Quality Content
- 60% Fewer Hallucinations
Browse by: Latest US Patents, China's latest patents, Technical Efficacy Thesaurus, Application Domain, Technology Topic, Popular Technical Reports.
© 2025 PatSnap. All rights reserved.Legal|Privacy policy|Modern Slavery Act Transparency Statement|Sitemap|About US| Contact US: help@patsnap.com