Detection method for detecting open-circuit fault of five-phase permanent magnet synchronous motor inverter
A permanent magnet synchronous motor, open-circuit fault technology, applied in the direction of measuring electrical variables, instruments, measuring electricity, etc., to achieve the effect of saving costs and increasing speed
- Summary
- Abstract
- Description
- Claims
- Application Information
AI Technical Summary
Problems solved by technology
Method used
Image
Examples
Embodiment 1
[0079] see Figure 4 ~ Figure 9 is the current waveform and the detection variable d after four types of faults occur in the motor n waveform.
[0080] The parameters of the five-phase permanent magnet synchronous motor in this embodiment are shown in Table 1:
[0081] Table 1 Parameters of five-phase permanent magnet synchronous motor
[0082]
[0083] The given rotational speed is 500rpm and the torque is 12Nm. Detection threshold k 1 =-1,k 2 =0.2,k 3 = 2.5.
[0084] Figure 4 is the current waveform of the motor after a single-tube, single-phase open-circuit fault occurs, Figure 5 is the detection variable d after the motor has a single-tube, single-phase open-circuit fault n The waveform:
[0085] When the motor is in 0.18~0.2s, d n About 1, fault indication D n =N, According to the fault indication signal, it is found that there is no open circuit fault, that is, the motor is running normally;
[0086] The motor can detect d after a period of time after 0...
Embodiment 2
[0096] Figure 10-11 After the motor speed changes, the current waveform and the detected variable d n waveform.
[0097] In this embodiment, the given five-phase permanent magnet synchronous motor torque is 12Nm. From 0 to 0.5s, the given speed is 700rpm. After 0.5s, the speed suddenly changes to 500rmp, and after 0.7s, the speed changes to 600rpm. The current waveform during the whole speed change process is as follows: Figure 10 shown. From Figure 11 It can be seen that although the detection variable has a small change in the process of the speed change, it does not affect the detection result, and after the speed is stable, the detection variable also returns to around 1, which shows that the change of the speed will not affect the fault detection. Results make a difference.
Embodiment 3
[0099] Figures 12 to 13 After the motor torque changes, the current waveform and the detected variable d n waveform.
[0100] In this embodiment, the given five-phase permanent magnet synchronous motor rotates at a speed of 500 rpm. The given torque is 3Nm from 0 to 0.5s, the torque suddenly changes to 12Nm after 0.5s, and the torque changes to 6Nm after 0.7s. The current waveform during the whole torque change process is as follows: Figure 12 shown. From Figure 13 It can be seen that although the detection variable has a small change during the torque change process, it does not affect the detection result, and after the torque is stable, the detection variable also returns to around 1, which shows that the torque change will not affect the fault detection results.
PUM
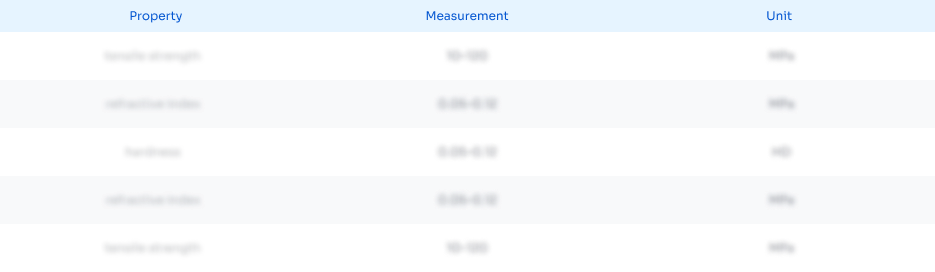
Abstract
Description
Claims
Application Information

- R&D Engineer
- R&D Manager
- IP Professional
- Industry Leading Data Capabilities
- Powerful AI technology
- Patent DNA Extraction
Browse by: Latest US Patents, China's latest patents, Technical Efficacy Thesaurus, Application Domain, Technology Topic, Popular Technical Reports.
© 2024 PatSnap. All rights reserved.Legal|Privacy policy|Modern Slavery Act Transparency Statement|Sitemap|About US| Contact US: help@patsnap.com