Method of preparing oxide dispersion strengthening medium-entropy alloy
A technology of dispersion strengthening and entropy alloying, which is applied in the field of preparation of medium-entropy alloy materials, can solve the problems of excessively large oxide particles, which have not been seen in literature reports, and achieve the effect of uniform distribution.
- Summary
- Abstract
- Description
- Claims
- Application Information
AI Technical Summary
Problems solved by technology
Method used
Image
Examples
Embodiment 1
[0021] 1. Weigh Cr, Ni, Co metal powders of equal atomic weight, choose coarse powder with a particle size of 45-20 μm for Ni, and fine powder with 10-5 μm for Co and Cr, and weigh 1.5wt% Y 2 o 3 powder, 0.4wt% Ti powder, Y 2 o 3 The nanometer powder of 30-20nm is selected, and the coarse powder of 45-30μm is selected as the Ti powder. After being fully mixed, the mixed powder is placed in a hydrogen reduction furnace for reduction at 400° C. for 1 hour.
[0022] 2. Under an argon atmosphere, encapsulate the alloyed metal powder in a ball mill jar with a ball-to-material ratio of 10:1, add 6wt% ethanol, fix the ball mill jar in a planetary ball mill, and mill at 350 rpm for 70 hours.
[0023] 3. The alloy powder after ball milling is sintered and formed in a spark plasma sintering furnace under the conditions of 1050°C, 50Mpa, and 8min.
[0024] 4. Under an inert atmosphere, heat-treat the sintered alloy ingot. The heat treatment conditions are 850°C, heat preservation for...
Embodiment 2
[0028] 1. Weigh Cr, Ni, Co metal powders of equal atomic weight, choose coarse powder with a particle size of 45-20 μm for Ni, and fine powder with 10-5 μm for Co and Cr, and weigh 1wt% Y 2 o 3 powder, 0.4wt% Ti powder, Y 2 o 3 The nanometer powder of 30-20nm is selected, and the coarse powder of 45-30μm is selected as the Ti powder. After being fully mixed, the mixed powder is placed in a hydrogen reduction furnace and reduced for 0.5h at 450°C.
[0029] 2. Under an argon atmosphere, encapsulate the alloyed metal powder in a ball mill jar with a ball-to-material ratio of 15:1, add 6wt% ethanol, fix the ball mill jar in a planetary ball mill, and mill at 300 rpm for 70 hours.
[0030] 3. The alloy powder after ball milling is sintered and formed in a spark plasma sintering furnace under the conditions of 1050°C, 50Mpa, and 8min.
[0031] 4. Under an inert atmosphere, heat-treat the sintered alloy ingot. The heat treatment conditions are 1050°C, heat preservation for 12h, a...
Embodiment 3
[0034] 1. Weigh Cr, Ni, Co metal powders of equal atomic weight, choose coarse powder with a particle size of 45-20 μm for Ni, and fine powder with 10-5 μm for Co and Cr, and weigh 1.5wt% Y 2 o 3 powder, 0.64wt% Ti powder, Y 2 o 3 The nanometer powder of 30-20nm is selected, and the coarse powder of 45-30μm is selected as the Ti powder. After being fully mixed, the mixed powder is placed in a hydrogen reduction furnace and reduced for 0.5h at 450°C.
[0035] 2. Under an argon atmosphere, encapsulate the alloyed metal powder in a ball mill jar with a ball-to-material ratio of 10:1, add 6wt% ethanol, fix the ball mill jar in a planetary ball mill, and mill at 300 rpm for 80 hours.
[0036] 3. The alloy powder after ball milling is sintered and formed in a spark plasma sintering furnace under the conditions of 1050°C, 50Mpa, and 8min.
[0037] 4. Under an inert atmosphere, heat-treat the sintered alloy ingot. The heat treatment conditions are 950°C, heat preservation for 18h,...
PUM
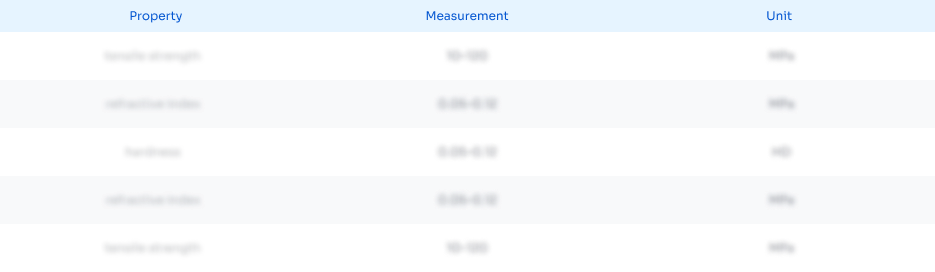
Abstract
Description
Claims
Application Information

- Generate Ideas
- Intellectual Property
- Life Sciences
- Materials
- Tech Scout
- Unparalleled Data Quality
- Higher Quality Content
- 60% Fewer Hallucinations
Browse by: Latest US Patents, China's latest patents, Technical Efficacy Thesaurus, Application Domain, Technology Topic, Popular Technical Reports.
© 2025 PatSnap. All rights reserved.Legal|Privacy policy|Modern Slavery Act Transparency Statement|Sitemap|About US| Contact US: help@patsnap.com