Hydrocracking catalyst and preparation method thereof
A hydrocracking and catalyst technology, which is applied in the direction of catalyst activation/preparation, physical/chemical process catalysts, molecular sieve catalysts, etc., can solve the problems of low activity of hydrocracking catalysts, achieve good industrial application prospects, high catalytic activity and activity Stable, easy-to-operate effects
- Summary
- Abstract
- Description
- Claims
- Application Information
AI Technical Summary
Problems solved by technology
Method used
Image
Examples
preparation example Construction
[0021] According to the preparation method of the hydrocracking catalyst provided by the present invention, the preparation method comprises the following steps:
[0022] (1) The water-soluble salt of the hydrogenation metal active component and the organic complexing agent are loaded on the carrier by the impregnation method, then dried and roasted to obtain a semi-finished catalyst, and the roasting conditions are such that the total amount of the semi-finished catalyst is used as a benchmark , the carbon content in the semi-finished catalyst is 0.03-0.5% by weight;
[0023] (2) using the solution containing the organic complexing agent as the impregnating liquid, the semi-finished catalyst obtained in step (1) is impregnated, then dried without roasting;
[0024] Wherein, the carrier contains inorganic heat-resistant oxides and macroporous molecular sieves.
[0025] According to the present invention, preferably, the calcination condition in step (1) is such that the carbo...
Embodiment approach
[0061] According to a preferred embodiment of the present invention, the inorganic heat-resistant oxide is alumina, and more preferably the carrier is alumina and a macroporous molecular sieve (ie, alumina-macroporous molecular sieve). Among them, alumina is more preferably alumina obtained after firing a hydrated alumina (aluminum hydroxide) colloidal compound.
[0062] According to a preferred embodiment of the present invention, based on the total amount of the carrier, the content of the macroporous molecular sieve in the carrier is 2-75% by weight, preferably 5-60% by weight, more preferably 5-40% by weight. % by weight, more preferably 5-30% by weight.
[0063] According to a preferred embodiment of the present invention, the carrier is alumina and macroporous molecular sieve, based on the total amount of the carrier, in the carrier, the content of macroporous molecular sieve is 2-75% by weight, preferably 5-60% by weight, more preferably 5-40% by weight, further prefer...
preparation example 1
[0080] (1) Get 200g dry base NaY molecular sieve (commercially purchased from Sinopec Changling Refining and Chemical Company Catalyst Factory, unit cell constant is The relative crystallinity is 100%, and the specific surface area is 720m 2 / g, sodium oxide content is 13.1% by weight) is placed in the reaction kettle, adds 200g ammonium sulfate and 2000mL water, with stirring temperature is raised to 90 ℃, and keeps 2 hours at this temperature. After the reaction, the reaction product was filtered, and the filter cake was washed with water three times to obtain molecular sieve NY-1.
[0081] (2) Take 100 grams of the molecular sieve NY-1 prepared in step (1), put it in a muffle furnace, feed water vapor while raising the temperature, raise the temperature to 550° C., keep the temperature for 2 hours, then cool down and take it out. The obtained product was placed in a reaction kettle, and 1000 mL of an aqueous solution containing sulfuric acid and ammonium sulfate was added...
PUM
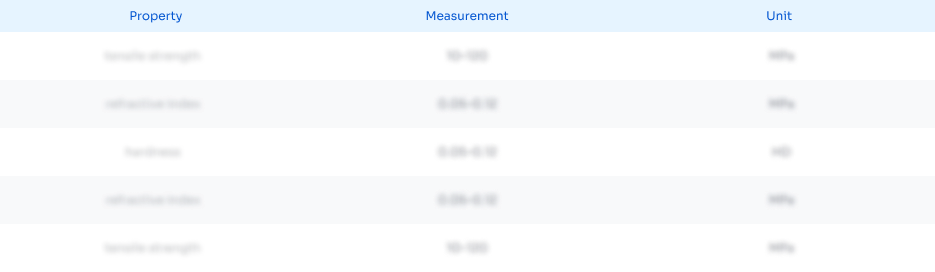
Abstract
Description
Claims
Application Information

- R&D Engineer
- R&D Manager
- IP Professional
- Industry Leading Data Capabilities
- Powerful AI technology
- Patent DNA Extraction
Browse by: Latest US Patents, China's latest patents, Technical Efficacy Thesaurus, Application Domain, Technology Topic, Popular Technical Reports.
© 2024 PatSnap. All rights reserved.Legal|Privacy policy|Modern Slavery Act Transparency Statement|Sitemap|About US| Contact US: help@patsnap.com