Method for preparing 3, 7-diethyl nonane-4, 6-diketone
A technology of ethyl nonane and diketone, applied in the field of organic chemical synthesis, can solve the problems of harsh reaction conditions, low yield and the like, and achieve the effects of low cost, safe yield and mild reaction conditions
- Summary
- Abstract
- Description
- Claims
- Application Information
AI Technical Summary
Problems solved by technology
Method used
Image
Examples
Embodiment 1
[0026] S1. Ethylmagnesium bromide (700ml, 5.5eq) was added to a three-necked flask, and a tetrahydrofuran (100g) solution containing dimethyl isophthalate (50g, 1.0eq) was added dropwise at 0°C. After the dropwise addition, the temperature was naturally raised to 25°C, and the system reacted for 2.5-4 hours. After the reaction, the reaction system was slowly poured into an aqueous ammonium chloride solution, and the product 2-3 was extracted with ethyl acetate (1000g), and the organic phase was concentrated to dryness. The residue was recrystallized from n-heptane to obtain 3,3'-(1,3-phenylene)bis(3-pentanol) with a yield of 76.8%.
[0027] S2. Dissolve the above 3,3'-(1,3-phenylene)bis(3-pentanol) (10g, 1.0eq) in acetic acid (50g), pour it into an autoclave, add 10% Pd / C (0.5g), replace with hydrogen, make the internal pressure 1.0-2.0MPa, heat the external bath to 100°C, react for 16h, after the reaction is completed, cool, filter, wash the filter cake with petroleum ether, ...
Embodiment 2
[0031] S1. Ethylmagnesium bromide (420ml, 5.5eq) was added to a three-necked flask, and a solution of tetrahydrofuran (50g) containing dimethyl isophthalate (30g, 1.0eq) was added dropwise at 0°C. After the dropwise addition, the temperature was naturally raised to 25° C., and the system reacted for 2.5-4 hours. After the reaction, the reaction system was slowly poured into an aqueous ammonium chloride solution, and the product 2-3 was extracted with ethyl acetate (600 g), and the organic phase was concentrated to dryness. The residue was recrystallized from n-heptane to obtain 3,3'-(1,3-phenylene)bis(3-pentanol) with a yield of 74.2%.
[0032] S2. Dissolve the above 3,3'-(1,3-phenylene)bis(3-pentanol) (30g, 1.0eq) in acetic acid (250g), pour it into an autoclave, add 10% Pd / C (5.5g), replace with hydrogen, make the internal pressure 1.5-2.0MPa, heat the external bath to 100°C, react for 16h, after the reaction is completed, cool, filter, wash the filter cake with petroleum et...
Embodiment 3
[0036]S1. Ethylmagnesium bromide (700ml, 5.5eq) was added to a three-necked flask, and a tetrahydrofuran (100g) solution containing dimethyl isophthalate (50g, 1.0eq) was added dropwise at 0°C. After the dropwise addition, the temperature was naturally raised to 25°C, and the system reacted for 2.5-4 hours. After the reaction, the reaction system was slowly poured into an aqueous ammonium chloride solution, and the product 2-3 was extracted with ethyl acetate (1000g), and the organic phase was concentrated to dryness. The residue was recrystallized from n-heptane to obtain 3,3'-(1,3-phenylene)bis(3-pentanol) with a yield of 76.8%.
[0037] S2. Dissolve the above 3,3'-(1,3-phenylene)bis(3-pentanol) (30g, 1.0eq) in acetic acid (200g), pour it into an autoclave, add 10% Pd / C (4.5g), replace with hydrogen, make the internal pressure 1.3-1.6MPa, heat the external bath to 100°C, react for 18h, after the reaction is completed, cool, filter, wash the filter cake with petroleum ether, ...
PUM
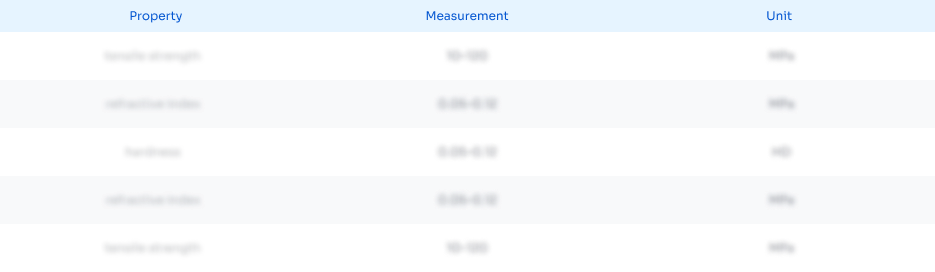
Abstract
Description
Claims
Application Information

- R&D
- Intellectual Property
- Life Sciences
- Materials
- Tech Scout
- Unparalleled Data Quality
- Higher Quality Content
- 60% Fewer Hallucinations
Browse by: Latest US Patents, China's latest patents, Technical Efficacy Thesaurus, Application Domain, Technology Topic, Popular Technical Reports.
© 2025 PatSnap. All rights reserved.Legal|Privacy policy|Modern Slavery Act Transparency Statement|Sitemap|About US| Contact US: help@patsnap.com