Silicon carbide polycrystalline shell-core wave-absorbing particles with graphene on surface, and preparation method and application thereof in textile finishing
A technology of graphene and silicon carbide, which is applied in the field of textile materials, can solve problems such as differences in absorbing performance, achieve good absorbing performance, excellent absorbing performance, and prevent secondary reflection pollution
- Summary
- Abstract
- Description
- Claims
- Application Information
AI Technical Summary
Problems solved by technology
Method used
Image
Examples
Embodiment 1
[0026] (1) Fully immerse the graphite paper electrode in 98% concentrated sulfuric acid, and ultrasonically treat it for 5 minutes to obtain a pretreated graphite paper electrode, and perform electrolysis of the pretreated graphite paper electrode at a voltage of 5V in 50% dilute sulfuric acid solution After reacting for 30s, take it out, wash it with water ultrasonically, and disperse it to obtain a 3 mg / mL graphene oxide solution.
[0027] (2) Add polycarbosilane to the graphene oxide solution, fully impregnate it, take it out, and dry it at 60°C to obtain graphene oxide pretreated polycarbosilane, wherein the graphene oxide pretreated polycarbosilane The content of graphene oxide is 0.01%.
[0028] (3) Put the polycarbosilane pretreated by graphene oxide in a horizontal tube furnace, first raise the temperature to 500°C at a rate of 10°C / min, keep it warm for 1h, and then raise the temperature to 1000°C at a rate of 5°C / min, Keep it warm for 30 minutes, then raise the temp...
Embodiment 2
[0031] (1) Fully immerse the graphite paper electrode in 98% concentrated sulfuric acid, and ultrasonically treat it for 10 minutes to obtain a pretreated graphite paper electrode, and perform electrolysis of the pretreated graphite paper electrode in 60% dilute sulfuric acid solution at a voltage of 8V After reacting for 90s, take it out, wash it with water ultrasonically, and disperse to obtain a 5mg / mL graphene oxide solution.
[0032] (2) Add polycarbosilane to the graphene oxide solution, fully impregnate it, take it out, and dry it at 90°C to obtain graphene oxide pretreated polycarbosilane, wherein the graphene oxide pretreated polycarbosilane The content of graphene oxide is 0.1%.
[0033] (3) Put the polycarbosilane pretreated by graphene oxide in a horizontal tube furnace, first raise the temperature to 500°C at a rate of 10°C / min, keep it warm for 1h, and then raise the temperature to 1000°C at a rate of 5°C / min, Keep it warm for 30 minutes, then raise the temperat...
Embodiment 3
[0036] (1) Fully immerse the graphite paper electrode in 98% concentrated sulfuric acid, and ultrasonically treat it for 6 minutes to obtain a pretreated graphite paper electrode, and perform electrolysis of the pretreated graphite paper electrode at a voltage of 6V in 55% dilute sulfuric acid solution After reacting for 60s, take it out, wash it with water ultrasonically, and disperse it to obtain a 4 mg / mL graphene oxide solution.
[0037] (2) Add polycarbosilane to the graphene oxide solution, fully impregnate it, take it out, and dry it at 80°C to obtain graphene oxide pretreated polycarbosilane, wherein the graphene oxide pretreated polycarbosilane The content of graphene oxide is 0.05%.
[0038] (3) Put the polycarbosilane pretreated by graphene oxide in a horizontal tube furnace, first raise the temperature to 500°C at a rate of 10°C / min, keep it warm for 1h, and then raise the temperature to 1000°C at a rate of 5°C / min, Keep it warm for 30 minutes, then raise the temp...
PUM
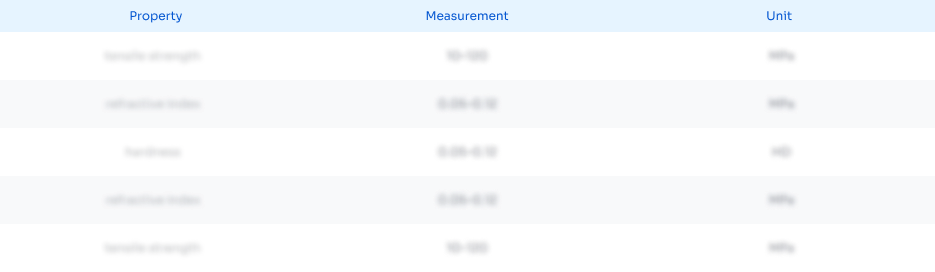
Abstract
Description
Claims
Application Information

- Generate Ideas
- Intellectual Property
- Life Sciences
- Materials
- Tech Scout
- Unparalleled Data Quality
- Higher Quality Content
- 60% Fewer Hallucinations
Browse by: Latest US Patents, China's latest patents, Technical Efficacy Thesaurus, Application Domain, Technology Topic, Popular Technical Reports.
© 2025 PatSnap. All rights reserved.Legal|Privacy policy|Modern Slavery Act Transparency Statement|Sitemap|About US| Contact US: help@patsnap.com