A kind of laser bronzing film for aluminum substrate and its production process and application
A technology of laser hot stamping film and production process, which is applied in the printing process, printing of special varieties of printed matter, adhesive type, etc. It can solve the problem of poor metal adhesion, insufficient corrosion resistance and wear resistance, and cannot be widely used. And other problems, to achieve good anti-adhesion, improve adhesion effect, good adhesion effect
- Summary
- Abstract
- Description
- Claims
- Application Information
AI Technical Summary
Problems solved by technology
Method used
Image
Examples
Embodiment 1
[0057]A laser bronzing film for an aluminum substrate in this embodiment comprises a PET film layer 1, a release layer 2, a wear-resistant resin layer 3, an aluminized layer 5 and an adhesive layer 6 which are stacked in sequence, wherein the release layer Layer 2 is composed of the following raw materials by weight percentage: melamine resin 15%, toluene 35%, butanone 50%; wherein, wear-resistant resin layer 3 is composed of the following raw materials by weight percentage: polymethyl methacrylate 60%, butanone 40%; wherein, the adhesive layer 6 is composed of the following raw materials in weight percentage: 30% of acrylic modified chlorinated polypropylene resin, 35% of ethylene glycol monobutyl ether, and 35% of ethylene glycol monobutyl ether acetate.
[0058] The production process of laser bronzing film for aluminum substrates is as follows:
[0059] (1) Prepare the release layer 2 coating: take melamine resin, toluene and methyl ethyl ketone respectively according to t...
Embodiment 2
[0067] A laser bronzing film for an aluminum substrate in this embodiment comprises a PET film layer 1, a release layer 2, a wear-resistant resin layer 3, an aluminized layer 5 and an adhesive layer 6 which are stacked in sequence, wherein the release layer Layer 2 is composed of the following raw materials by weight percentage: melamine resin 25%, toluene 15%, butanone 60%; wherein, wear-resistant resin layer 3 is composed of the following raw materials by weight percentage: polymethyl methacrylate 40%, butanone 60%; Wherein, the adhesive layer 6 is composed of the following raw materials in weight percentage: 40% of acrylic acid modified chlorinated polypropylene resin, 28% of ethylene glycol monobutyl ether, and 32% of ethylene glycol monobutyl ether acetate.
[0068] The production process of laser bronzing film for aluminum substrates is as follows:
[0069] (1) Prepare the release layer 2 coating: take melamine resin, toluene and methyl ethyl ketone respectively accordin...
Embodiment 3
[0077] A laser bronzing film for an aluminum substrate in this embodiment comprises a PET film layer 1, a release layer 2, a wear-resistant resin layer 3, an aluminized layer 5 and an adhesive layer 6 which are stacked in sequence, wherein the release layer Layer 2 is composed of the following raw materials by weight percentage: melamine resin 30%, toluene 30%, butanone 60%; wherein, wear-resistant resin layer 3 is composed of the following raw materials by weight percentage: polymethyl methacrylate 50%, butanone 50%; Wherein, the adhesive layer 6 is composed of the following raw materials in weight percentage: 40% of acrylic acid modified chlorinated polypropylene resin, 30% of ethylene glycol monobutyl ether, and 30% of ethylene glycol monobutyl ether acetate.
[0078] The production process of laser bronzing film for aluminum substrates is as follows:
[0079] (1) Prepare the release layer 2 coating: take melamine resin, toluene and methyl ethyl ketone respectively accordin...
PUM
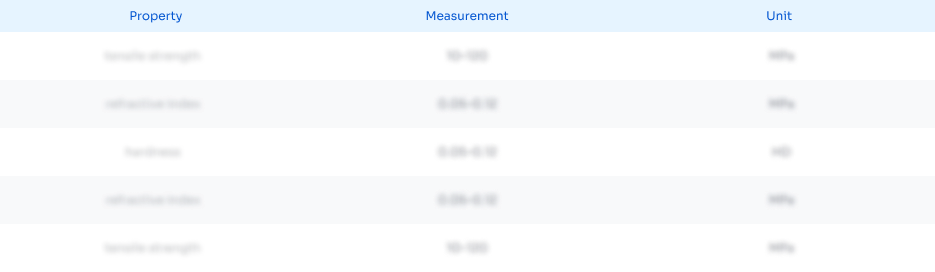
Abstract
Description
Claims
Application Information

- R&D
- Intellectual Property
- Life Sciences
- Materials
- Tech Scout
- Unparalleled Data Quality
- Higher Quality Content
- 60% Fewer Hallucinations
Browse by: Latest US Patents, China's latest patents, Technical Efficacy Thesaurus, Application Domain, Technology Topic, Popular Technical Reports.
© 2025 PatSnap. All rights reserved.Legal|Privacy policy|Modern Slavery Act Transparency Statement|Sitemap|About US| Contact US: help@patsnap.com