Technology for processing pre-sulphurized butyl rubber plate
A processing technology, vulcanized butyl technology, applied in the field of rubber, can solve the problems that natural rubber and butyl rubber cannot meet, and achieve the effects of long service life, convenient on-site maintenance and high air tightness
- Summary
- Abstract
- Description
- Claims
- Application Information
AI Technical Summary
Problems solved by technology
Method used
Examples
Embodiment 1
[0019] The composition of present embodiment pre-vulcanized butyl rubber sheet is as follows:
[0020] Butyl rubber raw material 1675N 21%, butyl rubber raw material 268 21%, activated magnesium oxide 0.4%, chlorinated paraffin 1.3%, polyethylene wax 1.3%, antioxidant RD 0.8%, antioxidant WB-16 1.3%, carbon black 770 7%, carbon black 66014%, talcum powder 7%, barium sulfate 13.3%, aromatic oil 2.7%, paraffin oil 300# 2.4%, transformer oil 1.7%, comaron 1.3%, zinc oxide 1.7%, sulfur 0.6 %, Accelerator DM 0.1%, Accelerator ZDC 0.8%, Accelerator NA-22 0.1%.
[0021] According to the above ratio, the butyl rubber raw material 1675N and the butyl rubber raw material 268 are stacked separately, and the active magnesium oxide, stearic acid, chlorinated paraffin, polyethylene wax, anti-aging agent RD, anti-aging agent WB-16, carbon black 770, carbon Black 660, talcum powder, barium sulfate, aromatic oil, paraffin oil 300#, transformer oil, comaron, and zinc oxide are stacked together...
Embodiment 2
[0028] The composition of present embodiment pre-vulcanized butyl rubber sheet is as follows:
[0029] Butyl rubber raw material 1675N 22%, butyl rubber raw material 268 22%, activated magnesium oxide 0.4%, chlorinated paraffin 1.3%, polyethylene wax 1.3%, antioxidant RD 0.8%, antioxidant WB-16 1.3%, carbon black 770 6%, carbon black 66013%, talcum powder 7%, barium sulfate 13.3%, aromatic oil 2.7%, paraffin oil 300# 2.4%, transformer oil 1.7%, comaron 1.3%, zinc oxide 1.7%, sulfur 0.6 %, Accelerator DM 0.1%, Accelerator ZDC 0.8%, Accelerator NA-22 0.1%.
[0030] According to the above ratio, the butyl rubber raw material 1675N and the butyl rubber raw material 268 are stacked separately, and the active magnesium oxide, stearic acid, chlorinated paraffin, polyethylene wax, anti-aging agent RD, anti-aging agent WB-16, carbon black 770, carbon Black 660, talcum powder, barium sulfate, aromatic oil, paraffin oil 300#, transformer oil, comaron, and zinc oxide are stacked together...
Embodiment 3
[0037] The composition of present embodiment pre-vulcanized butyl rubber sheet is as follows:
[0038] Butyl rubber raw material 1675N 20%, butyl rubber raw material 268 20%, activated magnesium oxide 0.4%, chlorinated paraffin 1.3%, polyethylene wax 1.3%, antioxidant RD 0.8%, antioxidant WB-16 1.3%, carbon black 770 7%, carbon black 66014%, talcum powder 8%, barium sulfate 14.3%, aromatic oil 2.7%, paraffin oil 300# 2.4%, transformer oil 1.7%, comaron 1.3%, zinc oxide 1.7%, sulfur 0.6 %, Accelerator DM 0.1%, Accelerator ZDC 0.8%, Accelerator NA-22 0.1%.
[0039] According to the above ratio, the butyl rubber raw material 1675N and the butyl rubber raw material 268 are stacked separately, and the active magnesium oxide, stearic acid, chlorinated paraffin, polyethylene wax, anti-aging agent RD, anti-aging agent WB-16, carbon black 770, carbon Black 660, talcum powder, barium sulfate, aromatic oil, paraffin oil 300#, transformer oil, comaron, and zinc oxide are stacked together...
PUM
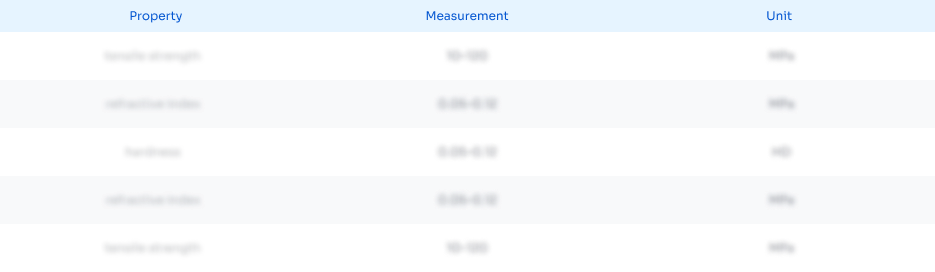
Abstract
Description
Claims
Application Information

- R&D
- Intellectual Property
- Life Sciences
- Materials
- Tech Scout
- Unparalleled Data Quality
- Higher Quality Content
- 60% Fewer Hallucinations
Browse by: Latest US Patents, China's latest patents, Technical Efficacy Thesaurus, Application Domain, Technology Topic, Popular Technical Reports.
© 2025 PatSnap. All rights reserved.Legal|Privacy policy|Modern Slavery Act Transparency Statement|Sitemap|About US| Contact US: help@patsnap.com