Ultrahigh-aluminium slag system for blast-furnace smelting
A blast furnace smelting and high-aluminum slag technology, applied in the field of iron and steel metallurgy, can solve problems affecting the production of special steel, and achieve the effects of increasing blast furnace permeability, reducing raw material costs, and improving slag stability
Inactive Publication Date: 2018-07-24
ANGANG STEEL CO LTD
View PDF2 Cites 2 Cited by
- Summary
- Abstract
- Description
- Claims
- Application Information
AI Technical Summary
Problems solved by technology
The disadvantages of the above-mentioned patents are that although the above-mentioned patents can reduce the viscosity of slag and improve the fluidity of slag, the B in iron ore
2
o
3
Not 100% into the slag, there is a part of B
2
o
3
It is reduced to B and enters the slag, which will affect the subsequent production of special steel
Method used
the structure of the environmentally friendly knitted fabric provided by the present invention; figure 2 Flow chart of the yarn wrapping machine for environmentally friendly knitted fabrics and storage devices; image 3 Is the parameter map of the yarn covering machine
View moreImage
Smart Image Click on the blue labels to locate them in the text.
Smart ImageViewing Examples
Examples
Experimental program
Comparison scheme
Effect test
Embodiment
[0027] The composition of the high-alumina slag system is shown in Table 1, wherein A1 is the composition of the high-alumina slag system produced by the existing blast furnace, and A2, A3, A4 and A5 are the composition of the high-alumina slag system of the embodiment of the present invention.
[0028] Table 1 Composition of high aluminum slag (wt,%)
[0029]
the structure of the environmentally friendly knitted fabric provided by the present invention; figure 2 Flow chart of the yarn wrapping machine for environmentally friendly knitted fabrics and storage devices; image 3 Is the parameter map of the yarn covering machine
Login to View More PUM
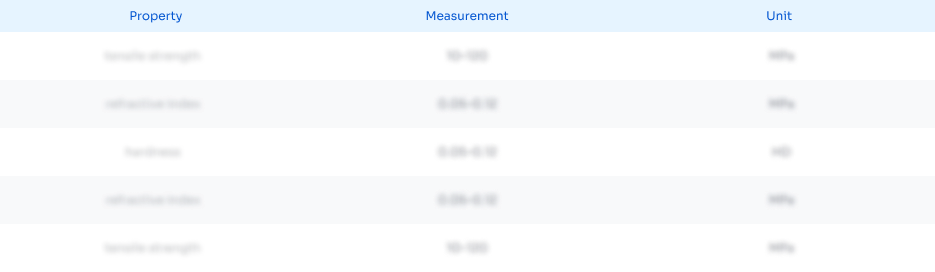
Abstract
The invention relates to an ultrahigh-aluminium slag system for blast-furnace smelting. The ultrahigh-aluminium slag system is prepared from the following components in percent by mass: 10-16% of MgO,18-30% of Al2O3, 1-5% of TiO2 and 0.7-1.15 of R2. When the content of Al2O3 in high aluminium slag of a blast furnace is 18-20%, the content of MgO is 10-12%, the content of TiO2 is 1-5%, and R2 is 1.05-1.10. When the content of Al2O3 in the high aluminium slag of the blast furnace is 20-23%, the content of MgO is 12-13%, the content of TiO2 is 2-5%, and R2 is 1.0-1.05. When the content of Al2O3in the high aluminium slag of the blast furnace is 23-25%, the content of MgO is 13-14.5%, the content of TiO2 is 3-5%, and R2 is 0.9-1.0. When the content of Al2O3 in the high aluminium slag of the blast furnace is 25-30%, the content of MgO is 14.5-16%, the content of TiO2 is 3-5%, and R2 is 0.8-0.9. The ultrahigh-aluminium slag system has the beneficial effects that the stability of the blast-furnace slag can be improved, and the defect of large fluctuation of the fluidity of the high-aluminium slag along with the temperature and the component is relieved; fluxing agents such as fluorite and manganese ore do not need to be added into blast-furnace materials, so that not only can the slag ratio be reduced and the air permeability of the blast furnace be further improved, but also erosionof the fluxing agents in the furnace slag to refractory materials in a hearth can be reduced.
Description
technical field [0001] The invention relates to the field of iron and steel metallurgy, in particular to an ultra-high aluminum slag system used in blast furnace smelting. Background technique [0002] Affected by overcapacity and other conditions in the iron and steel industry, the current market performance is sluggish. Therefore, cost reduction has become the primary task for the survival of iron and steel plants. However, when a large amount of high alumina ore is used in the blast furnace, the viscosity of the slag will increase, the blast furnace slag and iron will be difficult to tap, and the fuel consumption will increase. Therefore, in order to utilize a large amount of high alumina ore and effectively reduce the cost of blast furnace production, high alumina ore is basically used in conjunction with a large amount of low alumina ore, and finally the Al in the blast furnace slag 2 o 3 The content is controlled below 16%. But this kind of dilution "Al in the slag ...
Claims
the structure of the environmentally friendly knitted fabric provided by the present invention; figure 2 Flow chart of the yarn wrapping machine for environmentally friendly knitted fabrics and storage devices; image 3 Is the parameter map of the yarn covering machine
Login to View More Application Information
Patent Timeline

IPC IPC(8): C21B5/04
CPCC21B5/04
Inventor 姜喆刘杰车玉满孙鹏郭天永姚硕董刚王超蔡秋野武吉
Owner ANGANG STEEL CO LTD
Features
- R&D
- Intellectual Property
- Life Sciences
- Materials
- Tech Scout
Why Patsnap Eureka
- Unparalleled Data Quality
- Higher Quality Content
- 60% Fewer Hallucinations
Social media
Patsnap Eureka Blog
Learn More Browse by: Latest US Patents, China's latest patents, Technical Efficacy Thesaurus, Application Domain, Technology Topic, Popular Technical Reports.
© 2025 PatSnap. All rights reserved.Legal|Privacy policy|Modern Slavery Act Transparency Statement|Sitemap|About US| Contact US: help@patsnap.com