Efficient composite flocculant preparation method
A composite flocculant, high-efficiency technology, applied in chemical instruments and methods, flocculation/sedimentation water/sewage treatment, water/sewage treatment, etc., can solve the problem of insufficient removal speed of inorganic flocculants, and achieve excellent flocculation performance and settling speed Fast, wide-ranging effects
- Summary
- Abstract
- Description
- Claims
- Application Information
AI Technical Summary
Problems solved by technology
Method used
Image
Examples
Embodiment 1
[0028] S1: Take 100g of pottery clay and crush and grind it with a ball mill or a sand mill, pass all the solids through a 100-mesh sieve, put the qualified pottery clay in a muffle furnace, and calcinate at 750°C for 3 hours;
[0029] S2: Add hydrochloric acid with a mass fraction of 25% in the there-necked flask, raise the temperature to 120°C, add the calcined clay three times while stirring, the solid-liquid ratio is 1:5, and the reaction time is 3 hours, so that the aluminum and iron in the material Maximize the dissolution, filter while it is hot, test the aluminum and iron content of the liquid after cooling, and cool the solid for standby;
[0030] S3: adding an appropriate amount of aluminum hydroxide to the obtained aluminum ferric acid solution to adjust the aluminum content and pH, stirring and reacting at 120° C. for 3 hours, and cooling at room temperature for 24 hours after the reaction;
[0031] S4: Dry and weigh the solid after acid dissolution, put it into an...
Embodiment 2
[0036] S1: Take 100g of pottery clay and use a ball mill or sand mill to crush and grind all the solids through a 100-mesh sieve, put the qualified pottery clay in a muffle furnace, and calcinate at 760°C for 3 hours;
[0037] S2: Add hydrochloric acid with a mass fraction of 25% in the there-necked flask, raise the temperature to 120°C, add the calcined clay three times while stirring, the solid-liquid ratio is 1:5, and the reaction time is 3 hours, so that the aluminum and iron in the material Maximize the dissolution, filter while it is hot, test the aluminum and iron content of the liquid after cooling, and cool the solid for standby;
[0038] S3: adding an appropriate amount of aluminum hydroxide to the obtained aluminum ferric acid solution to adjust the aluminum content and pH, stirring and reacting at 120° C. for 3 hours, and cooling at room temperature for 24 hours after the reaction;
[0039] S4: Dry and weigh the solid after acid dissolution, put it into an autoclav...
Embodiment 3
[0044] S1: Take 100g of pottery clay and use a ball mill or a sand mill to crush and grind all the solids through a 100-mesh sieve, put the qualified pottery clay in a muffle furnace, and calcinate at 780°C for 3 hours;
[0045] S2: Add hydrochloric acid with a mass fraction of 25% in the there-necked flask, raise the temperature to 120°C, add the calcined clay three times while stirring, the solid-liquid ratio is 1:5, and the reaction time is 3 hours, so that the aluminum and iron in the material Maximize the dissolution, filter while it is hot, test the aluminum and iron content of the liquid after cooling, and cool the solid for standby;
[0046] S3: adding an appropriate amount of aluminum hydroxide to the obtained aluminum ferric acid solution to adjust the aluminum content and pH, stirring and reacting at 120° C. for 3 hours, and cooling at room temperature for 24 hours after the reaction;
[0047] S4: Dry and weigh the solid after acid dissolution, put it into an autocl...
PUM
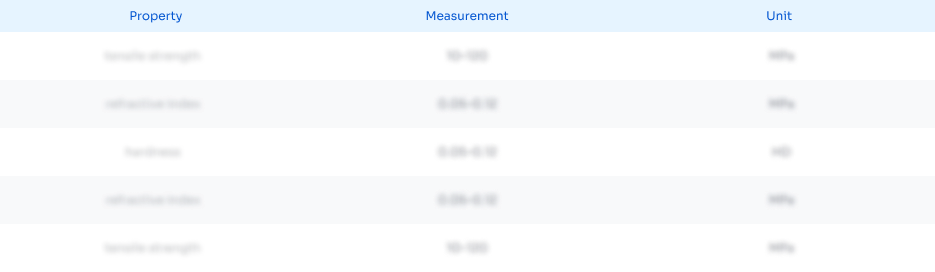
Abstract
Description
Claims
Application Information

- Generate Ideas
- Intellectual Property
- Life Sciences
- Materials
- Tech Scout
- Unparalleled Data Quality
- Higher Quality Content
- 60% Fewer Hallucinations
Browse by: Latest US Patents, China's latest patents, Technical Efficacy Thesaurus, Application Domain, Technology Topic, Popular Technical Reports.
© 2025 PatSnap. All rights reserved.Legal|Privacy policy|Modern Slavery Act Transparency Statement|Sitemap|About US| Contact US: help@patsnap.com