Preparation process of calcium carbonate
A preparation process and technology of calcium carbonate, applied in the direction of calcium carbonate/strontium/barium, etc., can solve the problems of low purity, low yield and low quality of calcium carbonate, and achieve high product purity, high yield and high quality. Effect
- Summary
- Abstract
- Description
- Claims
- Application Information
AI Technical Summary
Problems solved by technology
Method used
Image
Examples
Embodiment 1
[0028] The preparation technology of the calcium carbonate of the present embodiment, comprises the following steps:
[0029] (1) adding calcium nitrate to deionized water, dissolving and preparing a calcium nitrate solution with a mass fraction of 40%;
[0030] (2) Add ammonia water to the calcium nitrate solution at a temperature of 60° C., and add calcium hydroxide under strong alkaline pH conditions, stir evenly, let stand for 2 hours, and filter to obtain a refined solution;
[0031] (3) Ultrasonic atomize the refined solution into a refined atomized product, and pass the refined atomized product into the carbonization tower, then add ammonium bicarbonate to carry out carbonization reaction, control the carbonization temperature to 70 ° C, and the reaction time is 4 hours to obtain the intermediate product calcium carbonate materials;
[0032] (4) Add deionized calcium carbonate material to the intermediate product and heat it to 75°C, then add it into a stainless steel ...
Embodiment 2
[0042] The preparation technology of the calcium carbonate of the present embodiment, comprises the following steps:
[0043] (1) adding calcium nitrate to deionized water, dissolving and preparing a calcium nitrate solution with a mass fraction of 60%;
[0044] (2) Add ammonia water to the calcium nitrate solution at a temperature of 80° C., and ensure that the pH is strongly alkaline, add calcium hydroxide, stir evenly, let stand for 4 hours, and filter to obtain a refined solution;
[0045] (3) Ultrasonic atomize the refined solution into a refined atomized product, and pass the refined atomized product into the carbonization tower, then add ammonium bicarbonate to carry out carbonization reaction, control the carbonization temperature to 80 ° C, and the reaction time is 6 hours to obtain the intermediate product calcium carbonate materials;
[0046] (4) Add deionized calcium carbonate material to the intermediate product and heat it to 85°C, then put it into a stainless s...
Embodiment 3
[0056] The preparation technology of the calcium carbonate of the present embodiment, comprises the following steps:
[0057] (1) adding calcium nitrate to deionized water, dissolving and preparing a calcium nitrate solution with a mass fraction of 50%;
[0058] (2) Add ammonia water to the calcium nitrate solution under the temperature condition of 70° C., under the condition of ensuring pH strong alkalinity, add calcium hydroxide, stir evenly, let stand for 3 hours, and filter to obtain the refined solution;
[0059] (3) Ultrasonic atomize the refined solution into a refined atomized product, and pass the refined atomized product into the carbonization tower, then add ammonium bicarbonate to carry out carbonization reaction, control the carbonization temperature to 75 ° C, and the reaction time is 5 hours to obtain the intermediate product calcium carbonate materials;
[0060] (4) Add deionized calcium carbonate material to the intermediate product and heat it to 80°C, then...
PUM
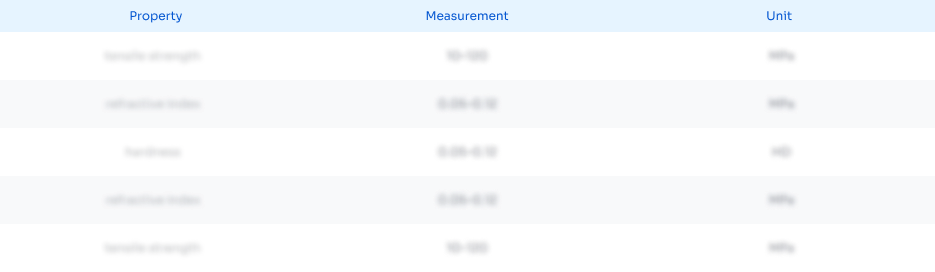
Abstract
Description
Claims
Application Information

- R&D
- Intellectual Property
- Life Sciences
- Materials
- Tech Scout
- Unparalleled Data Quality
- Higher Quality Content
- 60% Fewer Hallucinations
Browse by: Latest US Patents, China's latest patents, Technical Efficacy Thesaurus, Application Domain, Technology Topic, Popular Technical Reports.
© 2025 PatSnap. All rights reserved.Legal|Privacy policy|Modern Slavery Act Transparency Statement|Sitemap|About US| Contact US: help@patsnap.com