Production process for preparing high-iron-grade product and calcium magnesium acetate from RO-phase-containing material
A calcium magnesium acetate and production process technology, applied in the field of deep processing of steel slag, can solve the problems of low operating cost, failure to meet the requirements of the concentrate powder index, low grade iron containing RO phase, etc., and achieve low working conditions, good economic benefits, The effect of high market demand
- Summary
- Abstract
- Description
- Claims
- Application Information
AI Technical Summary
Problems solved by technology
Method used
Image
Examples
Embodiment Construction
[0025] The implementation of the present invention will be described in detail below in conjunction with the drawings and examples.
[0026] combine figure 1 Process flow of the present invention is described as follows:
[0027] Material A with RO phase content of 87.8%, its main chemical composition is FeO 53.2%, CaO 17.5%, MgO 14.0%, MnO 3.2%, SiO 2 4.8%, the iron grade of material A is 36.64%, and the fineness is -20μm. With 20% acetic acid solution, material A was mixed, stirred, and left to stand in step I. The operating parameters were as follows. The mixing ratio of material A and acetic acid solution was 20mL / g, and the temperature was stirred at 20°C for 7h, and the solution residue mixture was placed in After standing in the magnetic field for 3 hours, the layered supernatant of the mixture was completely clarified.
[0028] The precipitated clear mixture was isolated by filtration in step II. Pour out the supernatant in the mixture, and filter the precipitate ...
PUM
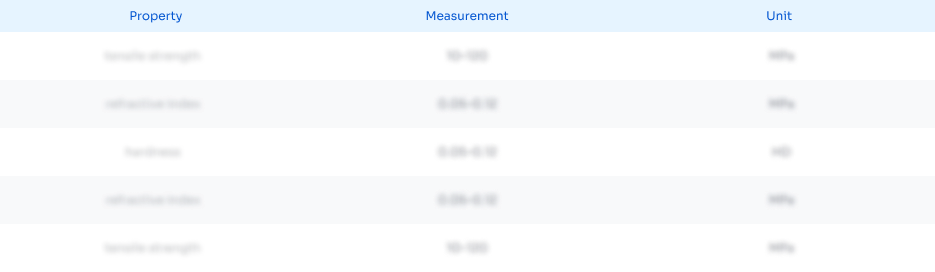
Abstract
Description
Claims
Application Information

- Generate Ideas
- Intellectual Property
- Life Sciences
- Materials
- Tech Scout
- Unparalleled Data Quality
- Higher Quality Content
- 60% Fewer Hallucinations
Browse by: Latest US Patents, China's latest patents, Technical Efficacy Thesaurus, Application Domain, Technology Topic, Popular Technical Reports.
© 2025 PatSnap. All rights reserved.Legal|Privacy policy|Modern Slavery Act Transparency Statement|Sitemap|About US| Contact US: help@patsnap.com