Air heating furnace
A hot blast stove, hot blast technology, applied in air heaters, fluid heaters, lighting and heating equipment, etc., can solve the problems of melting, polluting the environment, and insufficient combustion of fuel
- Summary
- Abstract
- Description
- Claims
- Application Information
AI Technical Summary
Problems solved by technology
Method used
Image
Examples
Embodiment Construction
[0018] Below, the present invention will be further described in conjunction with the accompanying drawings, so as to understand the technical idea of the present invention more clearly.
[0019] There is a feeding port on one side of the combustion chamber. Fuel (coal, biomass) first enters the side of the combustion chamber through the feeding port, vaporizes and burns, and then uses tools to move the unburned fuel to the interior of the combustion chamber. The air blown by the oxygen-assisted blower enters the combustion chamber and the slag-cleaning chamber respectively through the upper and lower oxygen-assisted air pipes, so that the fuel (coal, biomass) is fully contacted with oxygen, and the fuel (coal, biomass) is oxygenated twice to support combustion , to fully burn the fuel (coal, biomass). The energy utilization rate is improved, the black smoke phenomenon is basically eliminated, and the environmental pollution is reduced.
[0020] In the heat exchange chamber...
PUM
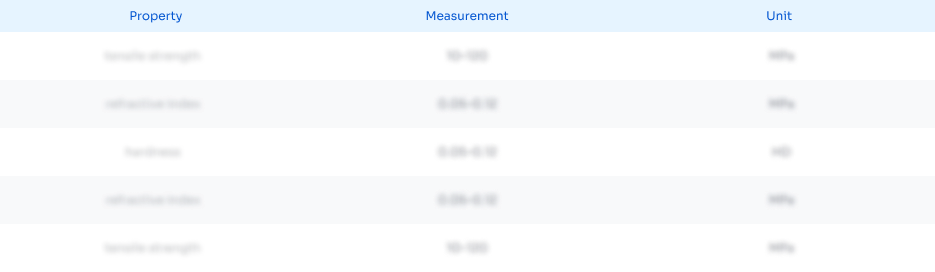
Abstract
Description
Claims
Application Information

- R&D Engineer
- R&D Manager
- IP Professional
- Industry Leading Data Capabilities
- Powerful AI technology
- Patent DNA Extraction
Browse by: Latest US Patents, China's latest patents, Technical Efficacy Thesaurus, Application Domain, Technology Topic, Popular Technical Reports.
© 2024 PatSnap. All rights reserved.Legal|Privacy policy|Modern Slavery Act Transparency Statement|Sitemap|About US| Contact US: help@patsnap.com