Polymer melt strength modifier and preparation method and application thereof, polypropylene composition and polypropylene material and preparation method thereof
A melt strength and modifier technology, applied in the field of polypropylene materials, can solve the problem of not giving melt strength measurement data, etc., and achieve the effect of improving melt strength and improving melt strength.
- Summary
- Abstract
- Description
- Claims
- Application Information
AI Technical Summary
Problems solved by technology
Method used
Image
Examples
preparation example Construction
[0023] As mentioned above, the present invention provides a method for preparing a polymer melt strength modifier, the method comprising: contacting polar monomer-grafted polypropylene with an amine-containing substance for reaction extrusion granulation, and then Drying; Wherein, the polar monomer can chemically react with the amine-containing substance, the amine-containing substance includes compound A and compound B, and the compound A is a compound containing an amine group, an ether bond and an aryl group The organic compound of the group, the compound B is a polyamine.
[0024] According to the preparation method of the present invention, the compound A is different from the compound B.
Embodiment approach
[0025] According to the preparation method of the present invention, the compound A that meets the aforementioned requirements can achieve the purpose of the present invention. According to a preferred embodiment of the present invention, the compound A is 4,4'-diaminodiphenyl ether, phenoxy One or more of phenylaniline, 3,4'-diaminodiphenyl ether and 3,3',4,4'-tetraaminodiphenyl ether, preferably the compound A is 4,4'-diamino One or more of diphenyl ether, 3,4'-diaminodiphenyl ether, 3,3',4,4'-tetraaminodiphenyl ether, more preferably the compound A is 4,4'- Diaminodiphenyl ether.
[0026] According to the preparation method of the present invention, the compound B that meets the aforementioned requirements can achieve the purpose of the present invention. According to a preferred embodiment of the present invention, the compound B is alkyldiamine, alkylenediamine, alkylene One or more of base triamine, alkylene tetramine, alkylene pentamine and aryl diamine; more preferabl...
Embodiment 1
[0046] Weigh 99 parts of maleic anhydride grafted polypropylene, 0.5 part of 4,4'-diaminodiphenyl ether, and 0.5 part of 1,12-diaminododecane, and mix well. The fully mixed raw materials are fed into the HAAKE twin-screw extruder. The heating section of the twin-screw extruder has 10 sections in total, the temperature of the first section is set at 160°C, and the temperature of the other sections is set at 190°C. Extruder speed 50r / min, feeding speed 3%. Extrude and granulate, and dry the obtained product at 90° C. for 30 minutes to obtain amine-modified polypropylene.
[0047] The resulting product was pressed into a film at a temperature of 200° C. and a pressure of 100 bar. The infrared spectrum analysis of the sample film was carried out by Shimadzu IRPresidge-21 Fourier transform infrared spectrometer. Infrared spectrum picture as figure 1 As shown, in the infrared spectrum, 1708cm -1 The imide characteristic peak generated by the reaction of maleic anhydride group ...
PUM
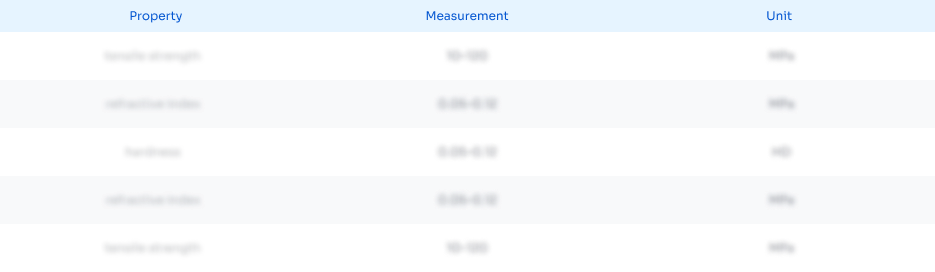
Abstract
Description
Claims
Application Information

- R&D
- Intellectual Property
- Life Sciences
- Materials
- Tech Scout
- Unparalleled Data Quality
- Higher Quality Content
- 60% Fewer Hallucinations
Browse by: Latest US Patents, China's latest patents, Technical Efficacy Thesaurus, Application Domain, Technology Topic, Popular Technical Reports.
© 2025 PatSnap. All rights reserved.Legal|Privacy policy|Modern Slavery Act Transparency Statement|Sitemap|About US| Contact US: help@patsnap.com