Method for improving rapid continuous casting tundish change success rate
A continuous casting tundish and tundish technology, which is applied in the field of steelmaking and continuous casting, can solve the problems of unspecified control range, hardening of the slab, production interruption, etc. cost effect
- Summary
- Abstract
- Description
- Claims
- Application Information
AI Technical Summary
Problems solved by technology
Method used
Examples
Embodiment 1
[0020] A method for improving the success rate of quick change of continuous casting tundish comprises the following steps:
[0021] Step 1: In the process of quick change of continuous casting tundish, the waiting time for the ladle filled with molten steel is 5-10min, and the temperature of the ladle reaches the continuous casting platform is 1590-1600°C;
[0022] Step 2: The casting speed of molten steel in the working tundish is reduced by one gear every 20 seconds, and the casting speed of the continuous casting machine is reduced to 0.3m / min within 8 minutes;
[0023] Step 3: Measure the liquid level of the working tundish. When the liquid level of the working tundish is 400mm, drive the spare tundish vehicle to the heat exchange preparation area. Simultaneously move to the other side;
[0024] Step 4: When the spare tundish car is driven to the pouring position, quickly install the red hot submerged nozzle, and the submerged nozzle baking time is ≥ 2 hours; adjust the ...
PUM
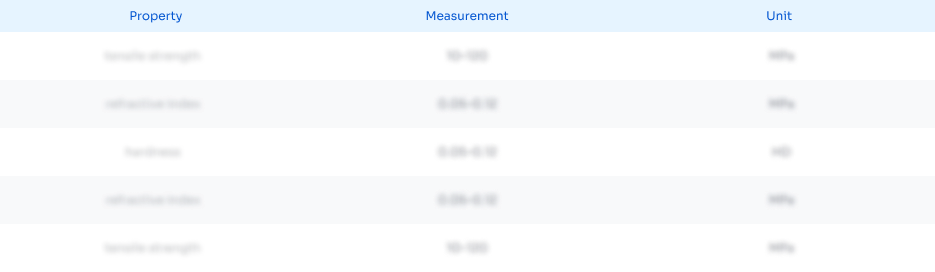
Abstract
Description
Claims
Application Information

- R&D
- Intellectual Property
- Life Sciences
- Materials
- Tech Scout
- Unparalleled Data Quality
- Higher Quality Content
- 60% Fewer Hallucinations
Browse by: Latest US Patents, China's latest patents, Technical Efficacy Thesaurus, Application Domain, Technology Topic, Popular Technical Reports.
© 2025 PatSnap. All rights reserved.Legal|Privacy policy|Modern Slavery Act Transparency Statement|Sitemap|About US| Contact US: help@patsnap.com