Method for producing chromium sesquioxide through chromium-rich sludge
A technology of chromium trioxide and sludge, which is applied in the direction of chromium trioxide, chromium oxide/hydrate, etc., can solve the problems of secondary pollution and low purity of chromium trioxide products, and achieve the effect of good quality and high purity
- Summary
- Abstract
- Description
- Claims
- Application Information
AI Technical Summary
Problems solved by technology
Method used
Examples
Embodiment 1
[0021] Embodiment 1, present embodiment provides a kind of method utilizing chromium-rich sludge to produce dichromium trioxide
[0022] First, wash and dry the chromium-containing sludge. The drying temperature is controlled at 200°C. This temperature can satisfy the drying of the sludge without changing the sludge. In this step, the main purpose of washing is to Large impurities in the sludge are washed out, for example, soluble salts.
[0023] Grind the dried sludge evenly, transfer it to a rotary calciner, use gas (mainly CO, H2) to directly heat it, and raise it to 530-570°C within 1.5-2 hours, then maintain the temperature for 1-1.5 hours, and then heat up The main purpose is to dehydrate the chromium hydroxide in the chromium-rich sludge to produce dichromium trioxide.
[0024] Then transfer to the cooling kiln to cool down to 60-90°C, add a certain amount of hydrochloric acid and water and stir for about 0.5 hours, add hydrochloric acid and water according to the rati...
Embodiment 2
[0030] Embodiment 2, present embodiment provides a kind of method utilizing chromium-rich sludge to produce dichromium trioxide
[0031] First, wash and dry the chromium-containing sludge. The drying temperature is controlled at 250°C. This temperature can satisfy the sludge drying without changing the sludge. In this step, the main purpose of water washing is to Large impurities in the sludge are washed out, for example, soluble salts.
[0032] Grind the dried sludge evenly, transfer it to a rotary calciner, use gas (mainly CO, H2) to directly heat it, and raise it to 530-570°C within 1.5-2 hours, then maintain the temperature for 1-1.5 hours, and then heat up The main purpose is to dehydrate the chromium hydroxide in the chromium-rich sludge to produce dichromium trioxide.
[0033] Then transfer to the cooling kiln to cool down to 60-90°C, add a certain amount of hydrochloric acid and water and stir for about 0.5 hours, add hydrochloric acid and water according to the ratio...
PUM
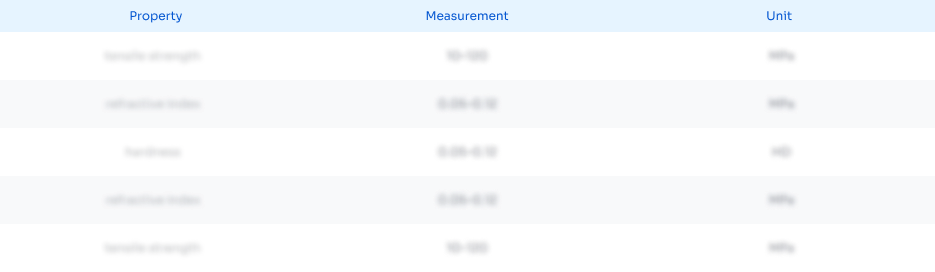
Abstract
Description
Claims
Application Information

- R&D
- Intellectual Property
- Life Sciences
- Materials
- Tech Scout
- Unparalleled Data Quality
- Higher Quality Content
- 60% Fewer Hallucinations
Browse by: Latest US Patents, China's latest patents, Technical Efficacy Thesaurus, Application Domain, Technology Topic, Popular Technical Reports.
© 2025 PatSnap. All rights reserved.Legal|Privacy policy|Modern Slavery Act Transparency Statement|Sitemap|About US| Contact US: help@patsnap.com