Gas injection device eliminating sidewind influence and injection method
A blowing device and gas technology, applied in the sintering field, can solve problems such as upward escape, potential safety hazards of personnel poisoning, uneven gas concentration, etc., and achieve the effects of reducing the channel area, improving the sintering effect, and increasing the channel area
- Summary
- Abstract
- Description
- Claims
- Application Information
AI Technical Summary
Problems solved by technology
Method used
Image
Examples
Embodiment approach
[0057] According to the first embodiment provided by the present invention, a gas injection device for eliminating the influence of side wind is provided.
[0058] A gas injection device for eliminating the influence of side wind, the device includes a sintering machine trolley 1, a gas injection device 2, and a spray cover 3. The sintering machine trolley 1 is located in the blowing hood 3 . The gas injection device 2 is located above the trolley 1 of the sintering machine. The two side wall panels of the blowing hood 3 are located on both sides of the sintering machine trolley 1 . The top of the spray cover 3 is a louver type anti-side wind roof device 4 . The louver-type crosswind-proof roof device 4 includes a connecting rod 401 and a louver 402 . One end of the connecting rod 401 protrudes from the side of the spray cover 3 . The louver 402 is connected with the connecting rod 401 .
[0059] In the present invention, the gas injection device 2 includes a gas injectio...
Embodiment 1
[0081] Such as figure 1 As shown, a gas injection device that eliminates the influence of side wind, the device includes a sintering machine trolley 1, a gas injection device 2, and a spray cover 3. The sintering machine trolley 1 is located in the blowing hood 3 . The gas injection device 2 is located above the trolley 1 of the sintering machine. The two side wall panels of the blowing hood 3 are located on both sides of the sintering machine trolley 1 . The top of the spray cover 3 is a louver type anti-side wind roof device 4 . The louver-type crosswind-proof roof device 4 includes a connecting rod 401 and a louver 402 . One end of the connecting rod 401 protrudes from the side of the spray cover 3 . The louver 402 is connected with the connecting rod 401 .
Embodiment 2
[0083] Such as figure 1 As shown, embodiment 1 is repeated, except that the gas injection device 2 includes a gas injection main pipe 201 , a gas injection branch pipe 202 , and a gas injection pipe 203 . The gas injection pipe 203 is arranged above the sintering machine trolley 1 , and the gas injection pipe 203 is located in the injection hood 3 . One end of the gas injection branch pipe 202 is connected to the gas injection main pipe 201 and the other end is connected to the gas injection pipe 203 . The device also includes rectifying means 5 . The rectifying device 5 includes a winch device 501 , a rope 502 , a fixed pulley 503 and a rectifying plate 504 . The capstan device 501 is arranged outside the blowing hood 3 . The fixed pulley 503 is arranged on the bottom surface of the louver type anti-side wind roof device 4 and is located directly above the gas injection pipe 203 . One end of the rope 502 is connected with the winch device 501 , and the other end of the r...
PUM
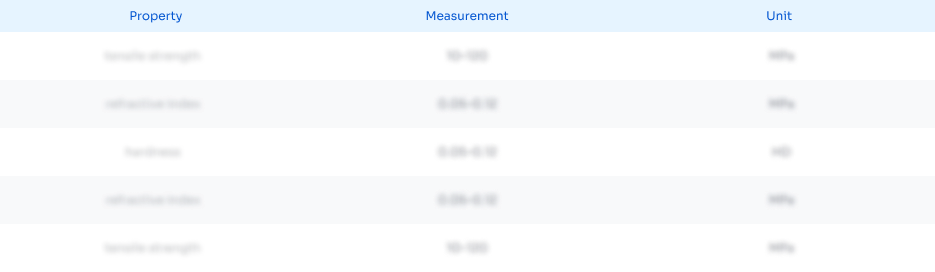
Abstract
Description
Claims
Application Information

- R&D Engineer
- R&D Manager
- IP Professional
- Industry Leading Data Capabilities
- Powerful AI technology
- Patent DNA Extraction
Browse by: Latest US Patents, China's latest patents, Technical Efficacy Thesaurus, Application Domain, Technology Topic, Popular Technical Reports.
© 2024 PatSnap. All rights reserved.Legal|Privacy policy|Modern Slavery Act Transparency Statement|Sitemap|About US| Contact US: help@patsnap.com