Punching die for camshaft bushing
A camshaft and bushing technology, which is applied in the field of mechanical processing, can solve problems such as low production efficiency, high processing cost, and affecting structure, and achieve the effects of improved processing efficiency, reduced processing cost, and accurate punching positioning
- Summary
- Abstract
- Description
- Claims
- Application Information
AI Technical Summary
Problems solved by technology
Method used
Image
Examples
Embodiment Construction
[0011] A punching die for a camshaft bushing of the present invention will be further described in detail below in conjunction with the accompanying drawings.
[0012] Figures 1 to 3 The punching die for the camshaft bush shown includes an upper die 2, a lower die, and a reset bracket. The upper die 2 is installed on the machine tool through the connecting plate 1. The bottom of the upper die 2 is set as a rectangular arc surface inwardly. The upper die 2 Waist circular groove 10 is set in the middle part of the arc surface of the bottom, the lower die includes punch 5, stripper plate 4 and punch seat 7, the cross section of punch 5 is set as waist circular, and the bottom waist of punch 5 and upper die 2 is round. The groove 10 is arranged correspondingly, the top surface of the punch 5 is set as an arc surface outward, the top surface of the stripper plate 4 is set as a rectangular arc surface outwardly, and a round through hole is set in the stripper plate 4, and the strip...
PUM
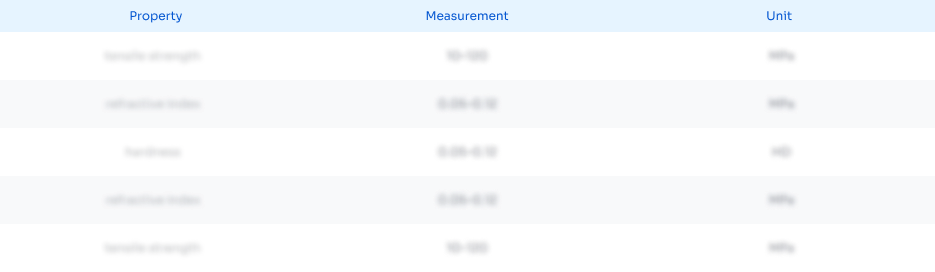
Abstract
Description
Claims
Application Information

- R&D Engineer
- R&D Manager
- IP Professional
- Industry Leading Data Capabilities
- Powerful AI technology
- Patent DNA Extraction
Browse by: Latest US Patents, China's latest patents, Technical Efficacy Thesaurus, Application Domain, Technology Topic, Popular Technical Reports.
© 2024 PatSnap. All rights reserved.Legal|Privacy policy|Modern Slavery Act Transparency Statement|Sitemap|About US| Contact US: help@patsnap.com