High-temperature-resistant wear-resistant lifter belt and preparation method thereof
A technology of high temperature resistance and hoist, applied in the field of rubber products, can solve the problems of short service life, damaged high temperature belt, single protective structure, etc., and achieve the effect of excellent wear resistance and tear resistance, and good temperature resistance.
- Summary
- Abstract
- Description
- Claims
- Application Information
AI Technical Summary
Problems solved by technology
Method used
Image
Examples
Embodiment 1
[0034] Such as Figure 1~2 As shown, a high temperature and wear-resistant hoist belt includes an upper cover rubber layer 1, an upper canvas layer 2, an upper steel mesh layer 4, a middle skeleton layer 5, a lower steel mesh layer 6, a lower canvas layer 7 and a lower cover rubber layer Layer 8: The high temperature and wear-resistant hoist belt is sequentially provided with an upper cover rubber layer 1, an upper canvas layer 2, an upper steel mesh layer 4, an intermediate skeleton layer 5, a lower steel mesh layer 6, and a lower canvas layer 7 and the lower cover glue layer 8.
[0035] It also includes an adhesive rubber layer 3; the upper and lower surfaces of the upper canvas layer 2 and the lower canvas layer 7 are compounded with a layer of adhesive rubber layer 3.
Embodiment 2
[0037] (1) Preparation of the upper cover rubber layer 1 and the lower cover rubber layer 8: the formula ratio is as follows in parts by weight, 100 parts of ethylene propylene rubber, 30 parts of carbon black N234, 15 parts of carbon black N220, and 2.5 parts of vulcanizing agent DCP Zinc oxide is 8 parts, stearic acid is 2 parts, accelerator TAIC is 2 parts, accelerator CZ is 1 part, antioxidant 4020 is 2 parts, antioxidant MB is 2 parts, paraffin oil is 10 parts, carbon 5 Petroleum resin is 3 parts, polytetrafluoroethylene is 25 parts, and basalt fiber is 2 parts. The above raw materials were kneaded at 130°C for 6 minutes, and then extruded at 50°C after standing for 8 hours to prepare a 10mm upper cover rubber layer 1 and a 5mm lower cover rubber layer 8.
[0038] (2) Preparation of the upper canvas layer 2 and the lower canvas layer 7: a high-temperature-resistant canvas woven with basalt fibers in the warp direction and polyester fibers in the weft direction;
[0039] ...
Embodiment 3
[0045](1) Preparation of the upper cover rubber layer 1 and the lower cover rubber layer 8: the formula ratio is as follows in parts by weight, 100 parts of ethylene propylene rubber, 40 parts of carbon black N234, 20 parts of carbon black N220, and 4 parts of vulcanizing agent DCP 2 parts of sulfur, 10 parts of zinc oxide, 2 parts of stearic acid, 2 parts of accelerator TAIC, 1 part of accelerator CZ, 2 parts of antioxidant 4020, 3 parts of antioxidant MB, paraffin oil 10 parts for carbon 5 petroleum resin, 10 parts for polytetrafluoroethylene, and 5 parts for basalt fiber. The above raw materials were kneaded at 155°C for 3 minutes, and then extruded at 80°C after standing for 16 hours to prepare a 10mm upper cover rubber layer 1 and a 5mm lower cover rubber layer 8 .
[0046] (2) Preparation of the upper canvas layer 2 and the lower canvas layer 7: a high-temperature-resistant canvas woven with aramid fiber in the warp direction and nylon fiber in the weft direction;
[00...
PUM
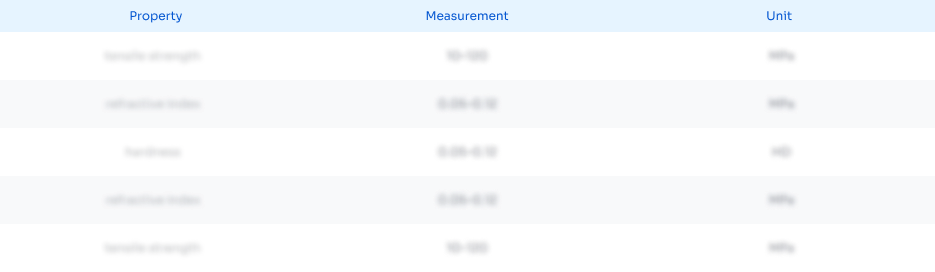
Abstract
Description
Claims
Application Information

- R&D
- Intellectual Property
- Life Sciences
- Materials
- Tech Scout
- Unparalleled Data Quality
- Higher Quality Content
- 60% Fewer Hallucinations
Browse by: Latest US Patents, China's latest patents, Technical Efficacy Thesaurus, Application Domain, Technology Topic, Popular Technical Reports.
© 2025 PatSnap. All rights reserved.Legal|Privacy policy|Modern Slavery Act Transparency Statement|Sitemap|About US| Contact US: help@patsnap.com