Synthetic method for high-capacity sulfurized lithium iron phosphate positive electrode material
A technology of lithium iron phosphate sulfide and cathode material, which is applied in battery electrodes, electrochemical generators, electrical components, etc., can solve the problems of low conductivity, affect performance capacity, and have not been solved, and achieve good conductivity and tight compounding. , the effect of structural stability
- Summary
- Abstract
- Description
- Claims
- Application Information
AI Technical Summary
Problems solved by technology
Method used
Examples
Embodiment 1
[0008] Embodiment 1 Take by weighing 84g of monohydrate lithium hydroxide, 115g of ammonium dihydrogen phosphate, 278g of ferrous sulfate heptahydrate, mix and stir evenly after being made into a solution, weigh 30g of monohydrate glucose and join in the sizing solution, and then weigh Take 1.6g Tween 20 and add it to the above slurry solution, disperse it by ball milling for 2 hours, and control the particle size in the slurry below 300nm. hours, the reaction slurry product was obtained, and the product was spray-dried under the protection of nitrogen to obtain a precursor material, which was sintered at 550° C. for 6 hours in a nitrogen atmosphere. After sintering, 16 g of glucose and 120 g of deionized water were added to the sintered material. After ball milling and dispersing for 3.5 hours, the slurry was spray-dried, and the dried material was sintered in a nitrogen atmosphere at 770°C for 8 hours to obtain a high-capacity lithium iron phosphate / lithium sulfide sulfur-car...
Embodiment 2
[0009] Example 2 Weigh 126g of lithium hydroxide monohydrate and 115g of ammonium dihydrogen phosphate, mix and stir evenly after making a 50% solution, weigh 120g of iron disulfide and add the above solution, after stirring evenly, weigh 20g of ascorbic acid and add it to the In the slurry solution, weigh 1.6g Tween 20 and add it to the above slurry solution, disperse it by ball milling for 2 hours, and control the particle size in the slurry to be below 200nm. After the ball milling, transfer the slurry into the hydrothermal reaction kettle, 110°C, hydrothermal reaction for 2 hours, the reaction slurry product was obtained, the product was spray-dried under the protection of nitrogen to obtain the precursor material, the precursor material was sintered at 450°C in nitrogen atmosphere for 2 hours, and 10g of glucose was added to the sintered material , add 120g of deionized water, disperse by ball milling for 3.5h, then spray dry the slurry, and sinter the dried material at 77...
Embodiment 3
[0010] Embodiment 3 Take lithium carbonate 74g, 85% phosphoric acid 116g, ferrous sulfate heptahydrate 278g, mix and stir after being made into 50% solution, weigh 15g of sucrose and join in the sizing solution, then weigh 1.6g Add Tween 20 to the above slurry solution, disperse by ball milling for 2 hours, and control the particle size in the slurry to be below 500nm. After the ball milling, transfer the slurry into a hydrothermal reaction kettle, and conduct a hydrothermal reaction at 105°C for 2 hours to obtain The slurry product of the reaction is spray-dried under the protection of nitrogen to obtain the precursor material. The precursor material is sintered at 550°C for 6 hours in a nitrogen atmosphere. After sintering, 32 g of glucose and 120 g of deionized water are added to the material, and the ball mill is dispersed for 4 hours. , and then the slurry was spray-dried, and the dried material was sintered at 770° C. in a nitrogen atmosphere for 8 hours to obtain a high-...
PUM
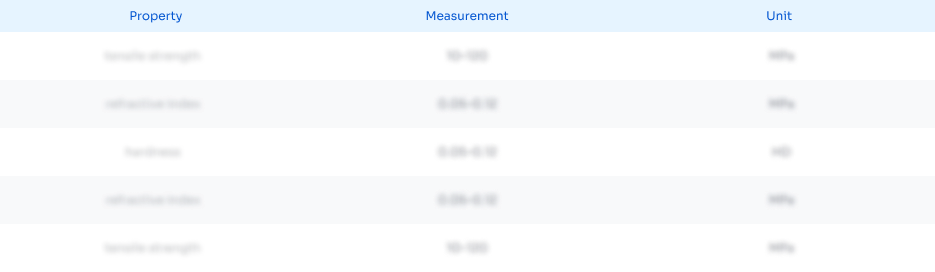
Abstract
Description
Claims
Application Information

- Generate Ideas
- Intellectual Property
- Life Sciences
- Materials
- Tech Scout
- Unparalleled Data Quality
- Higher Quality Content
- 60% Fewer Hallucinations
Browse by: Latest US Patents, China's latest patents, Technical Efficacy Thesaurus, Application Domain, Technology Topic, Popular Technical Reports.
© 2025 PatSnap. All rights reserved.Legal|Privacy policy|Modern Slavery Act Transparency Statement|Sitemap|About US| Contact US: help@patsnap.com