Method for preparing basic chromium sulfate from chromium plating sludge
A technology of chromium sulfate and sludge, which is applied in the field of waste resource utilization, can solve the problems of complicated process, increased recycling cost, and high chromium content in sludge, and achieves the effects of simple process flow, good economic benefits, and broad application prospects
- Summary
- Abstract
- Description
- Claims
- Application Information
AI Technical Summary
Problems solved by technology
Method used
Image
Examples
Embodiment 1
[0035] A kind of method utilizing chrome-plating sludge to prepare basic chromium sulfate, described method comprises the steps:
[0036] (1) According to the solid-to-liquid ratio of 1:6, the chromium-plating sludge is mixed with a sulfuric acid solution with a concentration of 10wt%, heated to 90° C. for leaching for 1 hour under stirring conditions, and filtered after the reaction is completed to obtain tailings and chromium-containing leachate;
[0037] (2) Under the condition of stirring, the pH of the chromium-containing leaching solution obtained by using sodium hydroxide solution to adjust step (1) is 3, and the liquid after filtering to obtain basic chromium sulfate and crystallization; Return to step (1) for the leaching of chrome-plating sludge.
[0038] After testing, the leaching rate of chromium is 92%, and the mass fraction of dichromium trioxide in basic chromium sulfate is 22.3%.
Embodiment 2
[0040] A kind of method utilizing chrome-plating sludge to prepare basic chromium sulfate, described method comprises the steps:
[0041] (1) According to the solid-to-liquid ratio of 1:4, the chrome-plated sludge is mixed with a sulfuric acid solution with a concentration of 30wt%, heated to 95° C. for leaching for 2 hours under stirring conditions, and filtered after the reaction is completed to obtain tailings and chromium-containing leachate;
[0042] (2) Under the condition of stirring, the pH of the chromium-containing leaching solution obtained by using sodium hydroxide solution to adjust step (1) is 3.5, and the liquid after filtering to obtain basic chromium sulfate and crystallization; Return to step (1) for the leaching of chrome-plating sludge.
[0043] After testing, the leaching rate of chromium is 95%, and the mass fraction of dichromium trioxide in the basic chromium sulfate is 20.6%.
Embodiment 3
[0045] A kind of method utilizing chrome-plating sludge to prepare basic chromium sulfate, described method comprises the steps:
[0046] (1) According to the solid-to-liquid ratio of 1:3, mix the chromium-plating sludge with a sulfuric acid solution with a concentration of 25wt%, heat it to 85°C for 1.5h under stirring conditions, filter after the reaction is completed, and obtain tailings and chromium-containing leachate ;
[0047] (2) Under the condition of stirring, the pH of the chromium-containing leaching solution obtained by using sodium hydroxide solution to adjust step (1) is 2.8, and the liquid after filtering to obtain basic chromium sulfate and crystallization; Return to step (1) for the leaching of chrome-plating sludge.
[0048] After testing, the leaching rate of chromium is 92.5%, and the mass fraction of dichromium trioxide in the basic chromium sulfate is 25%.
PUM
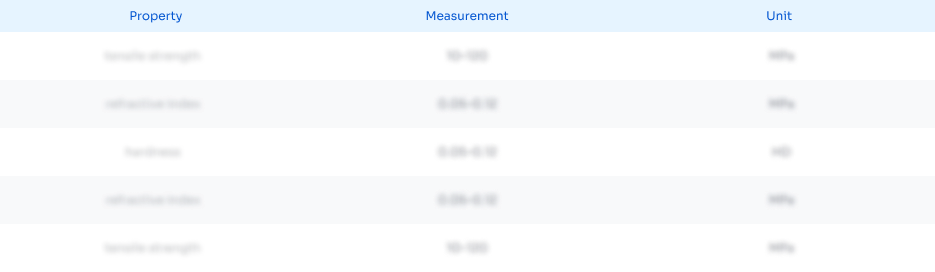
Abstract
Description
Claims
Application Information

- R&D Engineer
- R&D Manager
- IP Professional
- Industry Leading Data Capabilities
- Powerful AI technology
- Patent DNA Extraction
Browse by: Latest US Patents, China's latest patents, Technical Efficacy Thesaurus, Application Domain, Technology Topic, Popular Technical Reports.
© 2024 PatSnap. All rights reserved.Legal|Privacy policy|Modern Slavery Act Transparency Statement|Sitemap|About US| Contact US: help@patsnap.com