Method for leaching metal in vanadium titano-magnetite through full acid method
A technology of vanadium titanomagnetite and metal elements, applied in the direction of improving process efficiency, can solve problems such as low resource utilization rate, high technical difficulty, environmental pollution, etc., and achieve high resource utilization rate, increase specific surface area, and recovery effect. Good results
- Summary
- Abstract
- Description
- Claims
- Application Information
AI Technical Summary
Problems solved by technology
Method used
Image
Examples
Embodiment 1
[0039] Embodiment 1 vanadium-titanium magnetite leaching
[0040] The mineral of this embodiment is the vanadium-titanium magnetite concentrate of a certain mine in Xinjiang, and the ore contains vanadium, titanium, and iron at 0.538%, 3.24%, and 63.09%, respectively.
[0041] See figure 1 100g of the vanadium-titanium-magnetite concentrate is taken and ball milled with water in a three-roller four-barrel ball mill until the particle size of less than 0.074mm accounts for 60%. Take 20g of the ore sample after grinding for acid leaching, and use 100mL of 15% hydrofluoric acid in the first stage of leaching at 60°C for 3h with heating and stirring, the liquid-solid ratio is 1:5, and the stirring speed is 500rad / min.
[0042] After the leaching is completed, a vacuum pump is used to separate the solid and liquid to collect the leaching solution and leaching residue. The leaching solution is collected for use in the next process, and the leaching residue is subjected to secondar...
Embodiment 2
[0044] Embodiment 2 vanadium-titanium magnetite leaching
[0045] The mineral of this embodiment is the vanadium-titanium magnetite concentrate of a certain mine in Xinjiang, which contains vanadium, titanium, and iron at 0.869%, 5.46%, and 60.15%, respectively.
[0046]Take 100 g of the vanadium-titanium-magnetite concentrate and ball mill it with water in a three-roller and four-barrel ball mill until the particle size is less than 0.074mm and accounts for 80%. Take 100g of the ore sample after grinding and carry out full-acid leaching. A total of 200mL mixed acid of 5% hydrofluoric acid + 3% sulfuric acid + 2% hydrochloric acid is used for the first-stage leaching solution at 80°C. It is heated and stirred for 1h, and the liquid-solid ratio is 1: 2. The stirring speed is 800rad / min.
[0047] After the leaching is completed, a vacuum pump is used to separate the solid and liquid to collect the leaching solution and leaching residue. The leaching solution is collected for u...
Embodiment 3
[0049] Embodiment 3 ilmenite leaching
[0050] The mineral in this embodiment is the ilmenite concentrate of a mine in Panzhihua, which contains 9.38% and 57.26% of titanium and iron respectively.
[0051] Take 200g of the above-mentioned ilmenite concentrate and ball mill it with water in a three-roller four-barrel ball mill until the particle size is less than 0.074mm and accounts for 70%. Take 200g of the ore sample after grinding and carry out full-acid leaching. A total of 800mL mixed acid of 6% hydrofluoric acid + 3% sulfuric acid + 2% phosphoric acid is used for the first stage of leaching solution at 70°C. It is heated and stirred for 2h, and the liquid-solid ratio is 1: 4. The stirring speed is 600rad / min.
[0052] After the leaching is completed, a vacuum pump is used to separate the solid and liquid to collect the leaching solution and leaching residue. The leaching solution is collected for use in the next process, and the leaching residue is subjected to seconda...
PUM
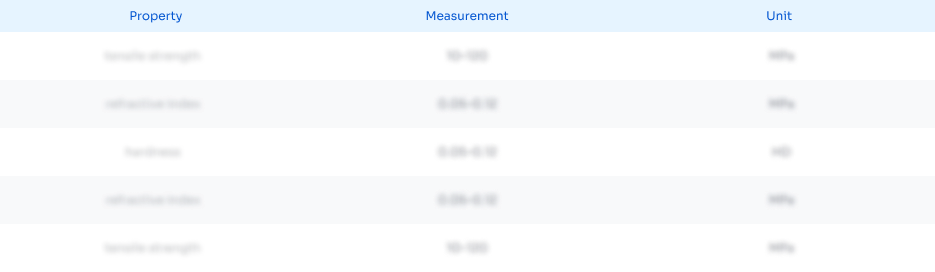
Abstract
Description
Claims
Application Information

- R&D
- Intellectual Property
- Life Sciences
- Materials
- Tech Scout
- Unparalleled Data Quality
- Higher Quality Content
- 60% Fewer Hallucinations
Browse by: Latest US Patents, China's latest patents, Technical Efficacy Thesaurus, Application Domain, Technology Topic, Popular Technical Reports.
© 2025 PatSnap. All rights reserved.Legal|Privacy policy|Modern Slavery Act Transparency Statement|Sitemap|About US| Contact US: help@patsnap.com