Sintering machine blowing device capable of adjusting blowing starting point in self-adaptation manner and blowing method thereof
A self-adaptive adjustment and injection device technology, applied in the field of sintering, can solve problems such as loss of auxiliary effect, safety accidents, gas fire, etc., and achieve the effects of strengthening auxiliary sintering effect, huge development potential, and improving safety factor
- Summary
- Abstract
- Description
- Claims
- Application Information
AI Technical Summary
Problems solved by technology
Method used
Image
Examples
Embodiment approach
[0067] According to the second embodiment provided by the present invention, a sintering machine injection method that can adaptively adjust the injection starting point is provided:
[0068] A sintering machine injection method capable of adaptively adjusting the starting point of injection or an injection method using the above-mentioned sintering machine injection device capable of adaptively adjusting the starting point of injection, the method comprising the following steps:
[0069] 1) The whole device starts to run, and the control system 9 monitors the temperature values of each bellows 4 in real time through the bellows temperature measuring device 5, and organizes the bellows temperature curve according to the temperature values of each bellows 4 measured by the bellows temperature measuring device 5. The position corresponding to the inflection point F is the best starting position for gas injection;
[0070] 2) During the real-time monitoring process, if the po...
Embodiment 1
[0078] like Figure 1-4 , Figure 6-9 As shown, a sintering machine injection device that can adaptively adjust the injection starting point, the device includes a sintering machine trolley 1, an injection cover 2, and a gas injection device 3. The gas injection device 3 includes a gas injection main pipe 301 , a gas injection branch pipe 302 , and a gas injection pipe row 303 . The sintering machine trolley 1 is located in the blowing hood 2 . The gas injection main pipe 301 is arranged on the outside of the injection cover 2 . The row of gas injection pipes 303 is arranged above the sintering machine trolley 1 , and the row of gas injection pipes 303 is located in the injection hood 2 . One end of the gas injection branch pipe 302 is connected to the gas injection main pipe 301 and the other end is connected to the gas injection pipe row 303 . The gas injection pipe row 303 includes a plurality of gas injection pipes 304 . The gas injection pipe 304 is provided with a g...
Embodiment 2
[0091] like Figure 1-3 , Figure 5-9 As shown, a sintering machine injection device that can adaptively adjust the injection starting point, the device includes a sintering machine trolley 1, an injection cover 2, and a gas injection device 3. The gas injection device 3 includes a gas injection main pipe 301 , a gas injection branch pipe 302 , and a gas injection pipe row 303 . The sintering machine trolley 1 is located in the blowing hood 2 . The gas injection main pipe 301 is arranged on the outside of the injection cover 2 . The row of gas injection pipes 303 is arranged above the sintering machine trolley 1 , and the row of gas injection pipes 303 is located in the injection hood 2 . One end of the gas injection branch pipe 302 is connected to the gas injection main pipe 301 and the other end is connected to the gas injection pipe row 303 . The gas injection pipe row 303 includes a plurality of gas injection pipes 304 . The gas injection pipe 304 is provided with a g...
PUM
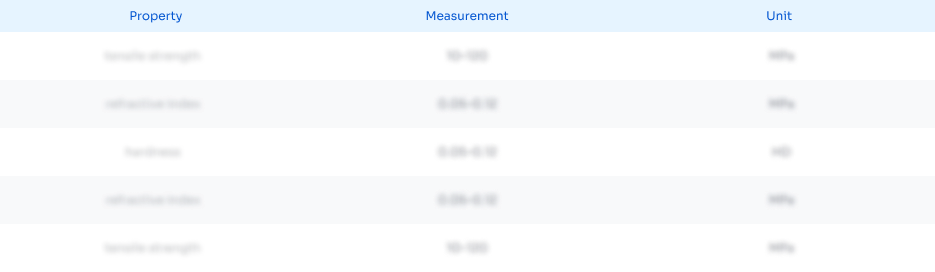
Abstract
Description
Claims
Application Information

- R&D Engineer
- R&D Manager
- IP Professional
- Industry Leading Data Capabilities
- Powerful AI technology
- Patent DNA Extraction
Browse by: Latest US Patents, China's latest patents, Technical Efficacy Thesaurus, Application Domain, Technology Topic, Popular Technical Reports.
© 2024 PatSnap. All rights reserved.Legal|Privacy policy|Modern Slavery Act Transparency Statement|Sitemap|About US| Contact US: help@patsnap.com