Preparation method of permanent magnet for transformer
A technology of permanent magnets and transformers, applied in the manufacture of inductors/transformers/magnets, magnetic objects, magnetic materials, etc., can solve problems such as insufficient magnetic properties, and achieve the effect of improving magnetic performance and corrosion resistance
- Summary
- Abstract
- Description
- Claims
- Application Information
AI Technical Summary
Problems solved by technology
Method used
Examples
Embodiment 1
[0006] A preparation method for a permanent magnet for a transformer, the steps are as follows: Weigh the following powders in parts by weight: 11 parts of neodymium, 50 parts of iron, 3 parts of boron, 1 part of rhodium, 1 part of palladium, 1 part of silver, 1 part of cerium, 2 parts of praseodymium, 3 parts of promethium, 1 part of samarium, 2 parts of europium, 3 parts of gadolinium, 1 part of dysprosium, 2 parts of holmium, mixed evenly to obtain a mixed powder, after drying the mixed powder in a vacuum oven, in argon atmosphere Under protection, the mixed powder is fully ball-milled and mixed with a high-energy ball mill, and then under a pressure of 20 MPa, the ball-milled mixed powder is hot-pressed and sintered at 550°C for 30 minutes, and then cooled in a furnace to obtain a permanent magnet for a transformer.
Embodiment 2
[0008] A preparation method for a permanent magnet for a transformer, the steps are as follows: Weigh the following powders in parts by weight: 12 parts of neodymium, 50 parts of iron, 3 parts of boron, 1 part of rhodium, 1 part of palladium, 1 part of silver, 1 part of cerium, 2 parts of praseodymium, 3 parts of promethium, 1 part of samarium, 2 parts of europium, 3 parts of gadolinium, 1 part of dysprosium, 2 parts of holmium, mixed evenly to obtain a mixed powder, after drying the mixed powder in a vacuum oven, in argon atmosphere Under protection, the mixed powder is fully ball-milled and mixed with a high-energy ball mill, and then under a pressure of 20 MPa, the ball-milled mixed powder is hot-pressed and sintered at 550°C for 30 minutes, and then cooled in a furnace to obtain a permanent magnet for a transformer.
Embodiment 3
[0010] A preparation method for a permanent magnet for a transformer, the steps are as follows: Weigh the following powders in parts by weight: 13 parts of neodymium, 50 parts of iron, 3 parts of boron, 1 part of rhodium, 1 part of palladium, 1 part of silver, 1 part of cerium, 2 parts of praseodymium, 3 parts of promethium, 1 part of samarium, 2 parts of europium, 3 parts of gadolinium, 1 part of dysprosium, 2 parts of holmium, mixed evenly to obtain a mixed powder, after drying the mixed powder in a vacuum oven, in argon atmosphere Under protection, the mixed powder is fully ball-milled and mixed with a high-energy ball mill, and then under a pressure of 20 MPa, the ball-milled mixed powder is hot-pressed and sintered at 550°C for 30 minutes, and then cooled in a furnace to obtain a permanent magnet for a transformer.
PUM
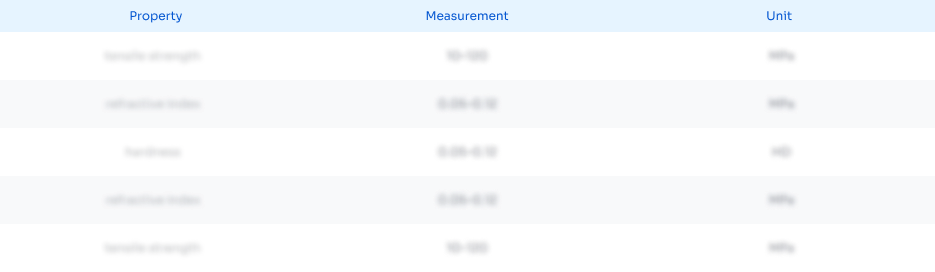
Abstract
Description
Claims
Application Information

- R&D Engineer
- R&D Manager
- IP Professional
- Industry Leading Data Capabilities
- Powerful AI technology
- Patent DNA Extraction
Browse by: Latest US Patents, China's latest patents, Technical Efficacy Thesaurus, Application Domain, Technology Topic, Popular Technical Reports.
© 2024 PatSnap. All rights reserved.Legal|Privacy policy|Modern Slavery Act Transparency Statement|Sitemap|About US| Contact US: help@patsnap.com