High efficiency production method of glycine
A production process, glycine technology, applied in the chemical industry, can solve the problems of difficult recycling of catalysts, limited industrial production value, freezing to -10°C, etc., and achieve the effects of facilitating recycling, increasing yield, and reducing production energy consumption
- Summary
- Abstract
- Description
- Claims
- Application Information
AI Technical Summary
Problems solved by technology
Method used
Examples
Embodiment 1
[0027] In a three-necked reaction flask equipped with a thermometer, a magnetic stirrer, a condenser tube and a dropping funnel, add 27.88 grams of 0.2500 mol of ammonium chloroacetate, 85.0 grams of methanol and 7.5 grams of urotropine, stir until completely dissolved, and heat up to At 60°C, 32.31 g (0.2500 mol) of N,N-diisopropylethylamine was slowly added dropwise, and the dropwise addition was completed within 2 hours, and then kept stirring at 67°C for 2.5 hours. Cool down to 50°C, filter the precipitated glycine crystals, and filter the mother liquor for the reaction in Example 2. The obtained glycine crystals were washed with methanol and dried to obtain 18.1 g of glycine crystals with a content of 98.5%, with a yield of 95.0%.
Embodiment 2
[0029] In the three-necked reaction flask that thermometer, magnetic stirrer, condensing tube and dropping funnel are housed, add respectively 27.88 grams (0.2500 moles) of ammonium chloroacetate, the filter mother liquor of embodiment one and add 0.8 grams of urotropine, stir Until it is completely dissolved, heat up to 63°C, start to slowly add 32.31 g (0.2500 mol) of N,N-diisopropylethylamine dropwise, and complete the dropwise addition within 2 hours, then keep stirring at 67°C for 2.5 hours. The temperature was lowered to 45° C., the precipitated glycine crystals were filtered, and the mother liquor was filtered for the third reaction in Example 3. The obtained glycine crystals were washed with methanol and dried to obtain 18.5 g of glycine crystals with a content of 98.2%, with a yield of 96.8%.
Embodiment 3
[0031] In a three-necked reaction flask equipped with a thermometer, a magnetic stirrer, a condenser and a dropping funnel, add 27.88 grams (0.2500 moles) of ammonium chloroacetate and the filtered mother liquor of Example 2 respectively, stir until completely dissolved, and heat up to 65°C , began to slowly add 32.31 g (0.2500 mol) of N,N-diisopropylethylamine dropwise, the dropwise addition was completed within 2 hours, and then kept stirring at 67°C for 2.5 hours. The temperature was lowered to 45° C., and the precipitated glycine crystals were filtered. The obtained glycine crystals were washed with methanol and dried to obtain 18.6 g of glycine crystals with a content of 98.0%, with a yield of 97.1%. Then, the temperature of the filtered mother liquor was lowered to 10° C., and 26.9 g of the precipitated N,N-diisopropylethylamine hydrochloride was filtered, and the filtered mother liquor was used for the reaction in Example 4.
PUM
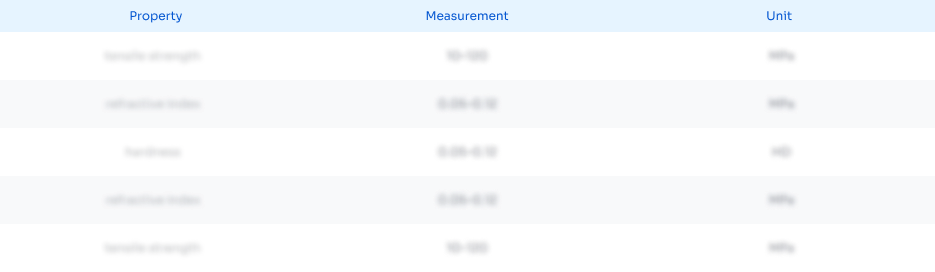
Abstract
Description
Claims
Application Information

- R&D Engineer
- R&D Manager
- IP Professional
- Industry Leading Data Capabilities
- Powerful AI technology
- Patent DNA Extraction
Browse by: Latest US Patents, China's latest patents, Technical Efficacy Thesaurus, Application Domain, Technology Topic, Popular Technical Reports.
© 2024 PatSnap. All rights reserved.Legal|Privacy policy|Modern Slavery Act Transparency Statement|Sitemap|About US| Contact US: help@patsnap.com