Injection moulding technology of glass fiber reinforced nylon component
An injection molding process, nylon technology, applied in coatings and other directions, can solve the problems of mechanical properties decline, fiber deformation, poor melt fluidity, etc., and achieve the effect of improving reinforcement and toughening efficiency, good rigidity, and uniform internal structure.
- Summary
- Abstract
- Description
- Claims
- Application Information
AI Technical Summary
Problems solved by technology
Method used
Examples
Embodiment Construction
[0018] An injection molding process for glass fiber reinforced nylon parts, including batching, mixing wax, mixing injection molding, cooling molding, wax removal and tempering;
[0019] Ingredients: Mix 98% nylon 66, 0.5% antioxidant, and 0.5% coupling agent evenly, then use a dehumidifier to dehumidify at 80°C for 3 hours to obtain nylon base material for use;
[0020] Waxing: heat the paraffin to 250°C, add chopped glass fiber after it is completely melted, stir and mix evenly, then keep warm to obtain a composite paraffin slurry for later use, wherein the mass ratio of chopped glass fiber to paraffin is 1:0.1;
[0021] Mixing injection molding: Send the nylon base material into the injection molding machine to heat up and melt, put the compound paraffin slurry into the preheated high-pressure grouting machine, turn on and off the injection molding machine and the high-pressure grouting machine at the same time, and mix the nylon base material melt and the high-pressure grou...
PUM
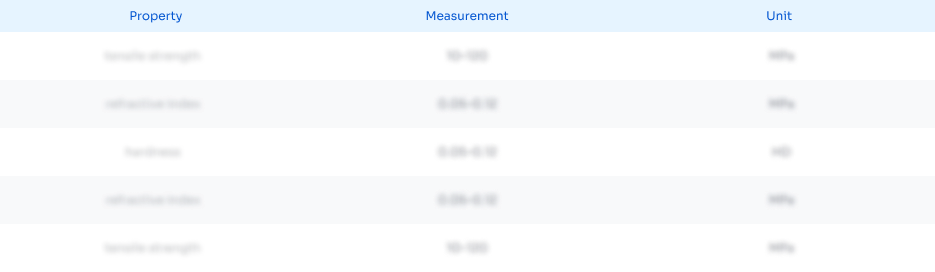
Abstract
Description
Claims
Application Information

- R&D
- Intellectual Property
- Life Sciences
- Materials
- Tech Scout
- Unparalleled Data Quality
- Higher Quality Content
- 60% Fewer Hallucinations
Browse by: Latest US Patents, China's latest patents, Technical Efficacy Thesaurus, Application Domain, Technology Topic, Popular Technical Reports.
© 2025 PatSnap. All rights reserved.Legal|Privacy policy|Modern Slavery Act Transparency Statement|Sitemap|About US| Contact US: help@patsnap.com